Фарфор. Начало. Отливка и шлифовка. (1)
Первый пост посвящен первому этапу работы с фарфором. Самому грязному и самому не творческому.Отливка и шлифовка, снова отливка и снова шлифовка… Потом утиль и шлифовка опять… Приступим. 🙂
Первые три дня получилось описать подробно…
27.07. 2016. Сегодня я приступила к работе. Вернее, впервые непосредственно соприкоснулась с самим материалом. До этого были только бесконечные подготовки. 🙂
Фарфор я купила в массе, проще говоря, в плюшке. Его нужно превратить в шликер, чтобы можно было лить. Я приобрела пару ведер с завинчивающейся крышкой и запаслась дистиллированной водой.
По совету друга [все благодарности всем за помощь я буду писать по окончании всей работы ;)], я налила в ведро некоторое количество воды, стала отрывать от плюшки небольшие куски и размывать их в воде. Очень аккуратно, чтобы не плескаться и не пускать пузыри. Отрывала сразу несколько кусочков, и пока один размывала (как будто намыливаешь мыло), остальные потихоньку размокали сами.
Занятие оказалось достаточно приятным, я бы сказала — медитативным, но не быстрым. Ведро объемом 3,2 литра, в итоге шликера намешалось примерно 2 литра. На это у меня ушло 3-3,5 часа тщательной и аккуратной работы.
Материал очень приятный на ощупь. Кусочки не склизские, а бархатистые, мягкие. Не выскальзывают из рук, а медленно размываются. И вода почему-то становится приятно теплой. В общем, хороший настрой для начала работы.
Меня не покидало осознание того, что я делаю всё-всё сама, от самого начала до самого конца — даже шликер не покупной, а собственноручно приготовленный. Так и чувствуешь, как с кончиков пальцев твоя энергетика переходит в материал… 🙂
После того, как шликер набрал консистенцию, примерно похожую на кефир, я закончила размешивание. Теперь нужно было процедить его от комочков, которые могли остаться на дне. Взяла второе ведро, натянула на него чулок и стала переливать… Надо было догадаться, что сухой капрон не мгновенно промокает… да и ведро держать было не очень удобно… Короче, я ливанула с ходу сильнее, чем рассчитывала и весь мой беспузырьковый шликер потек несколькими булькающими струйками. 🙂 Зато комочков оказалось очень мало. А на дне ведра вырисовался вот такой красивый рисунок из остаточных струек. Надеюсь, это добрый знак… 🙂 Кто умеет читать по «кофейной» гуще? :)) Я вижу дерево, а на донышке — деревья или кустарники. Может, это фарфоровые дебри, в которых я заблужусь? А может это знак растущего древа познаний, и через тернии к звездам…? :))
Промыла капрон, он стал влажным. Ополоснула первое ведро и занялась переливанием второй раз. В этот раз удачно и очень аккуратно. Визуально в шликере не было замечено ни одного пузырька.
Оставила отстаиваться до следующего дня.
Второй день работы — один из самых эмоционально насыщенных и впечатляющих дней, наверное… 🙂
Фарфор, на мой неопытный взгляд, отстоялся хорошо. Пузырьков не было видно ни на поверхности, ни в верхнем слое, ни на стенках или донышке. Зато он немного отслоился — на поверхности выступила вода, мм 3-5. Очень медленно и осторожно я заново его перемешала рукой (предварительно смочив на всякий случай руку, чтобы к ней не прицепились воздушные пузырьки). На дне, кстати, ощущалось что-то в роде очень мелкого песка, но визуально ничего ничего заметно не было.
Пока фарфор снова чуть отстаивался после перемешивания, я занялась чисткой форм перед отливкой. Открыла их первый раз после сушки. И тут меня ждали сюрпризы…
В массе гипса я увидела в некоторых местах ужасные ржавые пятнышки! В толще формы не страшно, но они обнаружились на стопе и попе.
В общем, я маленько запаниковала, опасаясь неприятных последствий на отливке. И решила выковырять этот ужас. Там оказалась маленькая (металлическая, наверное) песчинка, вокруг которой расползлась ржавчина. Откуда? Не знаю. Может в гипсовом порошке были, может с водой попали или еще как… Но штука явно нехорошая.
Может и не права, но вынула их и успокоилась. Зашкурить небольшой прыщик на попе будет просто, а вот если эта ржа попадет в фарфор, то, возможно, будет куда хуже…
Разобравшись с формами, собрав их обратно, я приготовилась к самому страшному и волнительному — отливке. Первой отливке фарфора. И, надо сказать, опасалась не напрасно…
Разложила необходимые инструменты и приготовила блокнотик. В него я записывала, какую форму во сколько залила, как и что происходило. В будущем мне так лучше будет понятно, откуда какой косяк взялся.
Хорошо проведенная отливка в совокупности с хорошо подготовленным шликером — залог того, что потом будет меньше косяков и переделок. Поэтому я быстро поняла — 70-80% деталей первой отливки точно пойдут в брак. :)) Ну, первый блин, как говорится… Делала-то я все правильно за исключением того, что правильно не получалось. И вся проблема состояла в том, что ни одна из приготовленных мною возможных емкостей для литья не работала так, как надо. Ни стаканчик с носиком (вроде бы правильным, а нет), ни мягкая пиала, ни обрезанный одноразовый стаканчик. .. А может просто руки корявые… :)) Все начиналось хорошо, а потом — опа! — и полилось по донышку, опрокинула чуть сильнее и вообще форму залила… В общем, разучилась явно, практики давно не было.
Надо лить быстро и точно, на донышко. У меня лилось как угодно — и по стенкам, и даже мимо. 🙂 Супер-дивайс от Маши Жуковой — лить по срезанной трубочке — тоже прокатил не очень (хотя, удобно, не спорю). Так как своими корявыми баночками и ручками я не могла попасть даже в соломинку. Использовать шприц для заливки маленьких форм у меня тоже пока не очень получилось (ничего не пузырилось, просто неудобно было). Я его использовала, но уже для подлива только, чтобы хоть как-то более-менее точно попадать.
Первая заливка прошла с очень переменным успехом. Маленькие формы я заливала, подливала по три раза, и не сливала вообще (также и с флюмо делала). Средние и большие решила сливать… но не вышло… То ли формы очень сухие (я их предварительно не увлажняла), то ли еще что… в общем, сливать было просто нечего. Несколько копель выцедила только из бедер и попы, даже грудь не слилась, не говоря уже о более мелких деталях. Так что они у меня просто перевернутые постояли и всё. Может, хоть стенки равномерные получились…
В шее маленький литник, поэтому грудь залить второй раз у меня не получилось. Второй раз заливала только попу. Все остальные детали залиты по одному разу.
Кстати говоря, смутили некоторые моменты (правда, не имеющие вроде бы последствий). В нескольких формах, особенно в маленьких, появились трещины в литниках. Я боялась, что трещины пойдут и по детали, но всё нормально. В основном трещины продольные, но были и поперечные, в горловине литника. Понятно, что дело в высыхании материала и усадке, но в том же флюмо никогда не встречала такого…
Кстати, с флюмо сравниваю не зря. Думаю, что тем, кто работает с флюмо и готовит себя к фарфору, может быть интересно. Материалы разные по многим ощущениям (в процессе отливки и обработки, потому что следующие этапы уже не сравнимы). Но я все же думаю, что пройдя флюмо, с фарфором работать будет легче, чем сразу лить из фарфора. Кому как, конечно. Но я рада, что уже имела дело с похожим материалом, потому что совсем не представляя как что делается, наверняка, наделала бы еще больше ошибок. Флюмо, безусловно, проще. Он как основа принципа работы.
Что еще заметила интересного. При заливке фарфора, особенно второй раз, потому что в первый шликер «убегает» внутрь очень быстро — внутри он начинает как-будто расслаиваться, отсекаться. Хотя перемешан был очень хорошо. Может это и есть наглядный принцип «черепкования»…? Но вот такая красота была замечена, и с тем же флюмо такого не видела.
Пока я все залила и убралась на столе после этого занятия, уже прошло больше трех часов и можно было начинать открывать первые маленькие формы.
Сразу скажу, что многие формы сильно передержала. Мне надо было на что-то ориентироваться в первый раз, и я прислушалась к советам коллег о примерном времени держания. Сколько держать отливку в форме — дело сугубо личное и зависящее от многих факторов: от увлажненности форм, от размера куклы и от размера форм, от влажности воздуха. .. от чего угодно. 🙂 Мне просто нужно было знать, что застывание черепка у фарфора происходит гораздо медленнее, чем у того же флюмо. Например, те же локти и коленки из флюмо я открывала уже минут через 20-25, а здесь точно надо ждать не меньше 2,5 часов.
Я решила, что лучше подольше, учитывая 90% влажность воздуха, ну и передержала в итоге. Форму надо открывать тогда, когда она открывается с небольшим усилием. Если надо прилагать много сил, то значит еще не досохло и можно или порвать отливку, или она осядет после открытия, т.к. еще очень мягкая. И открывать, естественно, очень осторожно и строго вертикально, без смещения, иначе можно что-то смазать.
Короче, начала открытия с самого первого, с локтей. И сразу вот такой интересный сюрприз. :))
Это называется — очень большой пузырь. :)) По какой-то причине отливка даже не сомкнулась, хотя я заливала литник до верху, подливала несколько раз, выгоняла пузыри и все делала правильно. Удивило и насмешило. 🙂
Сразу залила локти еще раз, и принялась открывать формы дальше.
Больше подобных сюрпризов не было. Но были на некоторых деталях поверхностные пузыри, и большие, и маленькие. Грешу на много вещей, в том числе и на «необкатанность» форм (ведь самая первая отливка). Поверхностный пузырь — это (наверное) когда воздух по какой-то причине зацепляется за внутренность формы в процессе заливки и прилипает к стенке. Такие пузыри не особо страшные. Их можно и нужно вскрыть, расковырять, увлажнить чуть-чуть и замазать фарфором, например, из литника. Только делать это надо, конечно, очень внимательно, чтобы под «заплаткой» не осталось воздуха. Но вот сколько пузырей могло попасть в толщу фарфора — секрет, который открывается только на высоком обжиге… и деталь идет в брак. Это мне предстоит узнать позже…
В общем, открывала по очереди формы, срезала литники, залепляла дырки от них и делала первичную сырую обработку деталек. Из обломов, помимо нескольких пузыриков, был один отломанный мизинец на кисти и отломанные пальцы на обеих стопах. 🙂
Надо сказать, что прилепляется фарфор очень хорошо. Если это сделать на совсем влажной отливке, то по внешнему виду — единое целое. И отломанные пальцы, и залепленные литники. А вот с залепленными пузырями чуть иначе оказалось, но об этом позже.
На первичную обработку коленей, кистей и стоп у меня ушло ровно три часа, и прежде чем открывать формы дальше, я взялась за переотлитые локти. Со второго раза все получилось хорошо.
Замазала литники, сделала прорези, отверстия под штифты, убрала швы. Но только с маленьких деталей. Закончила работу только в 11 вечера…
Предплечья, плечи, голени и бедра я просто достала из форм и положила в герметичный контейнер до завтра, чтобы не высыхали. Грудь и попу оставила до утра в формах.
Утром третьего дня в первую очередь открыла оставшиеся две большие формы. И поняла, что сильно передержала детали… А вот в контейнере отливочки замечательно дождались меня в сыроватом, почти свежевынутом виде.
О том, что такое передержка в моем понимании. В момент отливки образуется черепок, а потом он начинает сохнуть, уплотняться и, соответственно, уменьшаться в размерах. Идеально вынимать деталь надо, когда черепок уже достаточно прочный (не мягкий и не деформируется в руках, форма открывается легко), но еще не начал давать усадку. Но этот момент, как я уже писала, надо только чувствовать и подбирать время из личного опыта. У меня этого опыта пока не было.
Если деталь начинает усаживаться в форме, то она может деформироваться и застревать. Например, то же мизинец сломался у меня в самой форме, а не при вытаскивании. Это произошло, скорее всего, из-за того, что форма у него слишком изогнутая — ладонь начала усыхать и потащила за собой пальчики, а этот застрял в изгибе.
Второй момент — втулки шарнироприемников. Самый сложный момент, мне кажется. Деталь начинает давать усадку, а втулки не дают ей этого сделать. И получается, что отливка усаживается не равномерно — основная «свободная» масса уменьшается, а шарнироприемники остаются прежних размеров. Это нехорошо по двум причинам. Во-первых, деформируется деталь. А во-вторых, шарнироприемники потом могут оказаться великоватыми для шариков шарниров. В принципе, это можно будет убрать с помощью проклейки, но не всегда это будет красиво и точно.
На фото груди видны вмятины на лопатках. Их там быть не должно, лопатки у меня были сделаны гладкие. Это произошло из-за того, что я сделала достаточно глубокую втулку под грудной шарнир — деталь стала усыхать, а эта втулка не дала ей сделать это равномерно. Да, и еще почему-то оторвался кусок от спины… видимо тоже при уменьшении массы детали он, по какой-то непонятной причине, остался прилипшим к стенке формы…
На попе еще хуже, там получились откровенные вмятины, даже с заломами. Я могла бы грешить еще и на вакуум, который образуется, если при сливании формы она начинает булькать, и тогда еще мягкий черепок может отойти от стенок, втянувшись внутрь — но слив и залив был без единого плюха или булька. 🙂 Так что, скорее всего, такая деформация произошла как раз из-за бедренных втулок… хотя точно, конечно, сказать не могу. («Прыщик» на попе — это результат выковыривания ржавого пятна — легко убирается).
Такая же ерунда со втулками у меня произошла и с голенями, и с бедрами. Там просто видна «ступенька», где внутри заканчивалась втулка и начиналась свободная деталь.
Кстати говоря то, чего я боялась еще при самом литье — не оправдалось (по крайней мере пока). Много лилось по стенкам, почти все детали. Но ни одного потека на поверхности я не увидела. И некоторые формы, из-за все тех же кривых инструментов и рук, отливались медленно или вовсе с перерывами, но «годовых колец» или линий на отливках я также не увидела. А вот с тем же флюмо у меня такое было и ни раз, и заметно это уже на влажной или полусухой детали.
Теперь о моих возможных ошибках при обработке. Насколько они существенны — покажет высокий обжиг.
Я использовала много воды, хотя меня предупреждали, что делать этого не стоит. Работала по привычке, как делаю это при лепке. Пузыри или неровности я замазывала более мокрым фарфором, практически жижицей, а не массой из литника, которая близка по сухости самой отливке. Почему? Даже не знаю. Может так удобнее было, сподручнее при первой работе с материалом. А может потому, что мне интуитивно показалось, что более вязкая и жидкая масса лучше заполнит пустоту и застрахует меня от возможного остатка там воздуха. И сцепление лучше. Но вот какие результаты будут в итоге — увидим уже потом. Хотя на полусухих отливках более сырые места очень хорошо видны, выделяются серыми пятнами… Надеюсь их или контуры вокруг пятна не останется видно после обжига…
Кстати, хорошо видны на полусухом и швы. Швы, кстати, видны и на влажном. Там явно как-будто другая структура материала… И это меня очень настораживает, потому что я уже предвкушаю такие смачные полосы на красивых обожженных детальках… :))
Швы обрабатывала по-разному, и, возможно тоже наделала ошибок. Совсем низенькие и тоненькие я не срезала, а размывала кистью. Кисть, кстати, использовала резервуарную — очень удобная оказалась штука! Во-первых, сама она постоянно остается чуть влажной, не высыхает, а легкое нажатие на контейнер увлажняет ее сильнее, если это нужно; и не надо макать в воду. Во-вторых, у нее очень замечательная синтетическая щетина, не такая, как у обычных кисточек. Острый и мягкий кончик, и более толстая и жесткая середина — на все случаи жизни и степени нажатия. 🙂
Более высокие и широкие швы я срезала, а потом проходилась кистью сверху. Тут тоже надо угадать момент — слишком влажные швы при срезании липнут к ножу, тянутся за ним и оставляют «рваные раны», совсем сухие могут крошиться или откалываться. И еще под ними тоже могут скрываться коварные пузыри. Поэтому, чтобы была возможность хорошо залепить, надо срезать их на полусухих деталях, мне кажется. Зато стружка гладкая и хорошая, а если смочить ножик, то он за собой смазывает всё, подтирает. 🙂 Сверлить лучше влажную деталь и вручную. Она очень хорошо сверлится, мягко и четко, а если что-то откололось у краев вдруг — легко подлепить или размыть.
Кстати вот о размывке. Поняла, что с этим явно перестаралась. Ну, ничего — при следующей отливке буду работать иначе и посмотрю, как в итоге лучше. А беда была в том, что увлекшись увлажнением и размазыванием кистью неровностей, я «замыла» всю мою хорошенькую поверхность отливки. По сути надо было просто чуть подождать подсыхания швов, аккуратно их срезать и тонко пройтись кистью. Я же делала это размашисто, поэтому вся моя гладенькая отливочка снова стала полосатой и шероховатой от кисти, и ее всю заново надо будет шлифовать. Нет, дело-то не сложное, просто лишнюю работу себе подсунула. Ведь я очень хорошо выглаживала ММ, и шлифовать по сути нужно только сами швы и те небольшие пятнышки, где залепливался пузырик. Вот. 🙂
Сделала прорези, сгладила швы и залепленные литники, сделала все необходимые отверстия, и на этом пока отложила до полного высыхания. Каждый приспосабливается сам, что ему на каком этапе удобнее делать. Я общалась с фарфором первый раз и пока для себя не разобралась в этом. Что мне будет удобнее делать по-влажному, что на сушье, что на утиле. Утиль тоже еще надо понять, почувствовать — какая мягкость/жесткость/хрупкость, что возможно делать, что нет. Пока мне показалось, что основные операции удобнее делать по-влажному, а шлифовку и проработку деталей (ноготки, губки, четкость линий…), подгонку шарниров — по сухому. Говорят, что сухое очень хрупкое. Часть первых маленьких деталей у меня уже высохла, я попробовала поковырять ноготки на пальчиках стоп, и у меня не создалось впечатления хрупкости совершенно. Хотя детали все у меня получились очень толстостенными на мой взгляд. Наверное из-за того, что я не смогла ничего слить — всё по какой-то причине сразу хорошо впиталось. Следующий комплект попробую отливать немного иначе.
И еще о первых впечатлениях от материала.
Сразу при вынимании отливки из формы ощущается, что это совершенно иной материал, нежели флюмо. Не знаю как объяснить… И по тактильным ощущениям, и по звуку при срезании/прорезании ножом, по шуршанию кисти ощущаются словно мельчайшие песчинки, чувствуешь, что это керамика, «камень», а не пластик… Кстати, лезвие ножа оставляло серые следы на полусухой отлике. Это легко смывалось водой и, наверное, все сошлифуется… но эффект необычный. С флюмо такого не было, зато было точно также при обработке серебряной глины. 🙂
Пока материал мне понравился. Сухой он шлифуется очень мягко, даже слишком, и тут главное не переборщить. Пока этого не делала массово, просто попробовала на одной детальке. А вот расход материала мне показался большой. Опять же, может из-за моей косячной отливки. Но на один комплект у меня ушла почти половина разведенного шликера, а это не меньше литра… У флюмо точно гораздо меньший расход был. И, кстати — сухой фарфор гораздо легче флюмо, и это для меня было неожиданностью. Сырые детали тяжелые, а когда высыхают становятся очень легкими. Я ожидала камней, а он в таком виде скорее похож на высохший очень слабо разведенный гипс. Может так надо, не знаю… 🙂
Вот такие итоги трех рабочих дней — один полный комплект, который требует еще очень основательной шлифовки, проработки мелочей, финальной шлифовки утиля, и только потом пойдет на обжиг. Будущее время считать нехорошо, но предположу, что по самому минимуму при учете работы с утра до ночи (как обычно), уйдет еще не меньше дней 3-4х на это… Но спешить ни в коем случае нельзя. Это я поняла и почувствовала совершенно точно — фарфор спешки не любит и не простит.
Мне понравились все ощущения. Я очень люблю и влажную обработку, и шлифовку. Удручает только мысль, что твой труд может оказаться напрасным, если в толще фарфора засел злой пузырь, ждущий вылезти наружу и пустить твой труд, время и силы в мусор… Но это мы посмотрим. :)) Я морально готова к обломам, если что. Есть у меня уже подозрения на брак некоторых деталек, но я решила, что обжиг надо будет сделать всего — авось всё будет хорошо, а если брак — будет на чем тренироваться в росписи и пробовать краски. Всё в дело! 🙂
* * *
Дальше я буду писать уже не так подробно. Самые первые впечатления — самые яркие.
И писала я предыдущий текст сразу, по горячим следам. А дальше уже восстановленная, развернутая информация по кратким заметкам в блокнотике. Так что немного обобщу информацию. А то текст получится вообще необъятным. 🙂
Вся работа дальнейшая у меня заняла примерно месяц, не считая выходные, а именно рабочие дни. Работаю обычно с 10-11 часов утра до 7-9 часов вечера, с перерывом на перекус. В смысле, что это не 2-3 часа в день получается. :))
Следующие недели две вся работа была примерно одинаковая. Утром я делала отливку (уже не полностью весь комплект, а половину, а на следующий день вторую), потом днем я занималась обработкой и шлифовкой уже готовых деталек, а вечером открывала формы. Что-то обрабатывала сразу, что-то клала в контейнер до завтра. И так каждый день.
Расскажу, что происходило интересного, как искала оптимальные условия для работы, какие сделала выводы, какие ошибки, и всякие другие разности.
После своих первых мучений с емкостью для литья, я пошла в магазин и купила себе на пробу пластиковый кувшинчик с носиком. Это было единственное, что могло подойти. Объем большой, 1,4 литра. Но оказался он неожиданно очень хорошим! Просто идеальным для литья! Заливаю в него, конечно, немного и такой объем великоват, штука громоздкая вообще-то. Но дело не в этом, а в очень правильном носике. Он льет точно, не стекает по стенке, можно аккуратно регулировать струю до самой тоненькой. После моих первых мучений — великолепный вариант!
Еще расширила горлышки литников на некоторых деталях, в частности в шее. А в маленькие детальки (кисти, стопы, локти и колени) всё же более-менее приноровилась лить по трубочке, но из шприца. Напрямую из шприца мне неудобно (сложно контролировать нажатие), а кувшин слишком громоздкий, но по желобку из шприца получилось нормально.
Сливать не выходит всё равно. Думаю, что передерживаю. Хотя после заливки и нескольких подливок держу до переворачивания минут 5-10 примерно. Кое-что сливается — из попы, бедер и иногда голеней. Из груди так и не льется вообще, хотя деталь вроде бы большого объема. Большие заливаю второй раз, подождав еще минут 20 после переворачивания. Маленькие повторно не заливаю.
Первые заливки делала в сухие формы. Потом попробовала увлажнять их из пульверизатора дистиллированной водой с добавлением уксуса. Мне просто казалось, что формы и так весьма влажные — лью каждый день и влажность высокая. Но вот попробовала, и стало гораздо лучше. Даже не знаю, что именно изменилось, но чувствую, что лучше. 🙂
По времени выяснила для себя следующее. Маленькие детальки открываю через 2,5-3 часа, и нормально. Большие, соответственно, позже — пока постепенно обрабатываю мелкие, эти еще в формах. Но получается примерно так: предплечья, плечи и голени часа через 4,5-5, бедра, грудь и попу — через 6,5-8 часов. Головы, соответственно получается 5-6 часов.
ОТЛИВКА И ПЕРВАЯ ОБРАБОТКА
Теперь о странностях, ошибках и прочих казусах во время отливки. Без них никак! :))
Про вмятые детали я уже писала. С применением опрыскивания этого стало меньше, но всё равно какие-то проблемы остаются. Менее явные, но всё же. Спина продолжает немного оседать в лопатках (хотя я не булькаю, т.к. нечем, ничего не сливаю) и попа чуть-чуть проваливается. Вполне естественно получается, анатомично, но всё же не так, как должно быть.
Также попробовала сделать более жидкий шликер. Тоже вроде лучше стало…
Поверхностные пузыри уже упоминала тоже. Но вот в какой-то момент у меня получилось аж вот так. 0_0.
Причем и на попе (внизу детали), и на втулке «сыпь». Множество мельчайших пузырьков словно зацепились за форму или даже вышли из нее… Но этого быть не может. Что такое — не знаю. Встречаются периодически такие вещи (с уксусной водичкой меньше), но чтобы в таком количестве…
Еще интересная штука — вот такое «отслоение». Вынула детальку и долго думала, как же это так могло получиться? И вообще что это? По стенке не лилось точно. Воронка литника не отставала от стенок, чтобы при втором заливе могло что-то попасть…
Срезала, сошлифовала — не считая этой странности, форма детали никак не деформирована. Т.е. убрала этот наплыв и как ничего и не было…
Самыми сложными на этапе литья стали кисти, ну, и стопы.
На стопах упорно отламывались все пальцы при открытии форм (или до). Но я потом устранила возможную причину (чуть подточила форму) и стало лучше.
А вот с пальцами кистей что-то не так. Открываю форму и вижу вот такие оторванные хлопья. То есть внутри как будто какие-то слоистые пустоты. При вынимании и открытии отрываются куски и сами пальцы словно разрывает на две части, иногда по шву даже видна щель.
Пробовала разное. Открывала формы еще сырыми, т.е. рано. Специально передерживала в формах, чтобы высохло получше и совсем легко открылось и уселось. Увлажняла уксусной водой. Лила на сухую. По-всякому, короче, но эффект примерно одинаковый — чуть лучше, чуть хуже. Лучше, если открыть еще сыроватые формы, перед отливкой их хорошо спрыснуть водой. Но всё равно, хоть от одно пальчика, но кусочек оторвется. То у шва, то на костяшке, то снизу, то кончик…
Предположение есть, но странное, потому что не знаю, есть ли у кого еще такое и возможно ли это. Мне кажется, что очень сильно тянет форма. Пространство маленькое и естественно пальцы не получаются полыми. Но, видимо, тенденция есть и при высыхании уже, когда всё впиталось, но еще черепкуется (уплотняется), пальчик всё еще тянет к стенкам формы. И разрывает. Бред? Не знаю. Но явно есть продольная рваная щель…
Чистила форму. Думала, может липкая какая и при открытии что-то прилипает, что-то легко отходит… Думала, может это я разрываю ее при открытии. Но специально пробовала подержать подольше и открывала именно когда уже совсем без усилий… Думала, может еще швы большие получились — они как-то застревают, растягивают и пр…
Короче, не знаю… Промазывала щель и отслоения водой, плотно сжимала, где нужно наращивала, проглаживала сверху… Визуально ничего не видно потом, ни во влажном, ни в сухом виде. А есть ли там воздух — покажет высокий обжиг… сломав мне все пальцы. =D
Пальцы ломала неоднократно. И в формах, бывало, треснувшие уже (мизинцы в основном), и при вынимании что-то в форме оставалось, и при обработке уже. Приклеивала элементарно и следов не оставалось никаких. Говорят, их даже специально мастера ломают, чтобы позы изменить. 🙂 Я позы меняла, но по-другому. Я проходилась по поверхности свежевынутой детальки влажной кистью и пальчик сразу становился мягким. Чуть гнула или распрямляла его в нужную позу. Не знаю, правильно или нет, но пока последствий не видела. И каждая кисть у меня получилась пусть чуть-чуть, но отличающаяся от других.
Уже писала выше, но повторюсь. Очень понравилось обрабатывать детальки по-сырому или по полусухому. Если жестковато, что чуть увлажнить и снова податливый материал. Для больших плоскостей и заглаживания швов использовала резервуарную кисть. Для мелочей, как пальчики или лицо — сначала основное делала кисточкой из колонка, пожестче, потом совсем мокрой кистью уже по чуть подсохшей детальке проходилась мягкой белочкой. Поверхность получается очень ровная, дальнейшая шлифовка почти не нужна, только уже самое-самое финишное выглаживание чуть-чуть. Даю подсохнуть после последнего увлажнения, чтобы деталь была жесткой и «бледнела». И потом осторожно прохожусь мелкой шкуркой. Поверхность прям шелковистая выходит.
Это вот шлифовка по полусырому. Очень гладенько получается. И шлифуется приятно, пыли очень мало и она не разлетается, а смахивается кистью. Только использовать надо не совсем полировочную шкурку, а чуть покрупнее. Тогда она именно шлифует, а не смазывает, но следов и царапин не оставляет.
Еще про формы пару слов. Про ржавые пятна было выше. Также на влажных формах хорошо видны мелкие черные песчинки. Просеивание гипса ничего не дает, они очень мелкие. Раньше, кстати, такого не наблюдала, а в этот раз вроде купила тот же самый гипс, а тут такая фигня. В общем, эти песчинки постепенно вылезают из самого гипса, вытягиваются. То есть, переходят из формы в отливку. И получаются черные вкрапления на поверхности детальки и мелкие выемки на форме. При следующих отливках, когда песчинок уже нет, получается вот такой эффект мурашек на теле. 🙂 Но мне кажется, что это плохо. Боюсь, что за эти микродырочки в гипсе может «цепляться» воздух и увеличивать вероятность поверхностных пузырьков. ..
Вот что меня, кажется, обошло пока стороной (тьфу-тьфу-тьфу), так это «слои» — поперечные полосы по детальке. Это когда льешь слишком медленно. Получаются такие «годовые кольца». Вот с этим не столкнулась. Хотя, опять же сравню, с флюмо было сплошь и рядом. Убираются, правда, легко. Но всё равно. Хоть что-то мне пока не досталось… :))
Какие могу подвести итоги этой части работы?
+ Естественно, шликер должен быть хороший — это залог многих успехов. Однородный, хорошо процеженный и размешанный, и главное — без пузырей. Вот в чем почти очень уверена, так это в шликере. Мне кажется, что он был вполне хороший, по крайней мере — сделанный на совесть. 🙂
+ Густоту шликера каждый подбирает сам. Мне удобнее пожиже.
+ Сливать очень аккуратно, медленно, не булькая, т.е. не давая дырочки литника полностью закрыться. При узких горлышках это бывает нелегко. Поэтому некоторые литники я расширяла.
+ Заливку делаю так. Увлажняю формы из пульверизатора, быстро закрываю и сразу лью. Достаточно быстро стараюсь, но аккуратно, чтобы струя по-возможности сразу попала на донышко, а не лилась по стенкам. Дальше слежу внимательно, как уходит из литника шликер. В мелких детальках он очень быстро убегает. Как близится к самому узкому месту, но еще не перешел границу (иначе воздух попадет или при узком отверстии просто не зальется больше) — подливаю опять до полного литника. И так 3-5 раз. Потом оставляю минут на 5-10, иногда 15, в зависимости от детали. Потом сливаю (если получается). Сливаю теперь так: медленно наклоняю форму, пока не покажется капелька. Оставляю в таком положении на несколько минуток, потом поворачиваю на 90 гр, оставляя такое же наклонное положение. И так, пока не пройду весь круг. Мне кажется, что так получаются более равномерные стенки. Дальше сливаю, если что-то еще осталось. Потом еще чуть-чуть жду и в самые большие детали заливаю еще один раз. Потом сливаю и оставляю стоять вверх ногами.
+ Увлажнение формы водой с уксусом дает положительные результаты — меньше поверхностных пузырей, деталька меньше деформируется и хорошо отходит от формы.
+ Обрабатывать удобнее всего по-сырому и полусухому. По-максимуму делать всё: прорези, отверстия, залеплять литники и срезать швы — однозначно. Корректировать положение пальцев, обрабатывать швы и первично шлифовать. Вода хорошо разглаживает, мягкая шкурка делает почти идеальную поверхность. Удобно использовать резервуарную кисть, а также мелкие кисточки разной жесткости. Проработку тоже удобнее делать на этом этапе — всегда можно сгладить слишком резкую борозду от шила или ножа, что-то подлепить. Мало пыли. Деталь не хрупкая, хотя с ней надо тоже быть осторожной.
+ Если что-то сломалось, на влажном или полусухом всегда можно еще починить — прилепить палец или замазать пузырь.
+ С применением коробочек, где деталь остается влажной — работать очень удобно и практично. Не надо торопиться обрабатывать сразу; деталька остается в нужном состоянии достаточно долго.
Продолжение поста: http://nastasia-mirror.livejournal.com/125554.html
Толкачева_Общие вопросы.
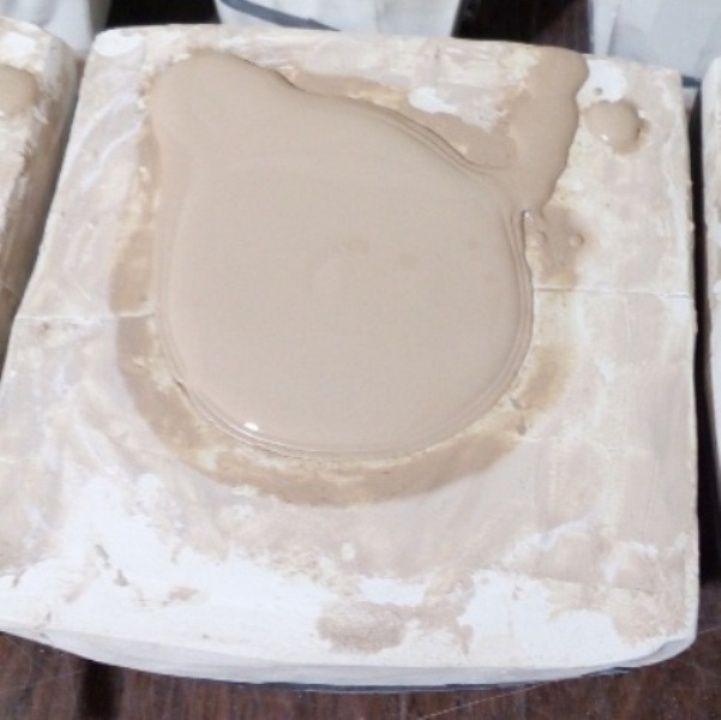
%PDF-1.3 % 1 0 obj >]/Pages 3 0 R/Type/Catalog/ViewerPreferences>>> endobj 2 0 obj >stream 2018-06-25T11:28:44+05:002018-06-25T11:28:58+05:002018-06-25T11:28:58+05:00Adobe InDesign CS6 (Windows)uuid:3c97c7aa-401c-4f0b-b7c2-560a0d5dbfcfxmp.did:BF81B306D74DE411B24FB20E6B9967A1xmp.id:D8E5F88B4078E811BA32A7853EAA1E70proof:pdf1xmp.iid:D6E5F88B4078E811BA32A7853EAA1E70xmp.did:E3B0011FA439E5118436ED2ED37270DDxmp.did:BF81B306D74DE411B24FB20E6B9967A1default
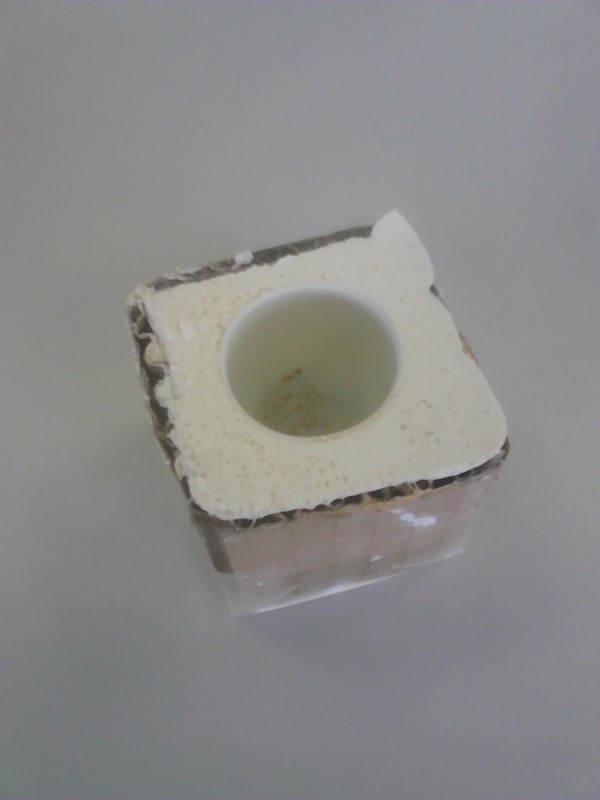
От шликера до «бисквита».

Императорский фарфоровый завод был основан во время правления Елизаветы Петровны. Тогда в 1744 году он стал первым фарфоровым предприятиям в стране. Изначально на заводе изготавливались только мелкие предметы и аксессуары, но со временем производство стало расширяться. В настоящее время здесь выпускается более полутора миллиона изделий в год – четыре тысячи разных наименований. Для изготовления фарфора мастера уже используют современные технологии – 3d-моделирование, растровую печать и компьютерный дизайн. Директор ИФЗ Татьяна Тылевич рассказала, чем живет завод в наши дни.
Как из шликера сделать «бисквит»
На Императорском фарфоровом заводе трудятся более тысячи мастеров. Ежедневно они превращают шликер – жидкую серую массу – в настоящее произведение искусства, фарфоровые изделия. Сначала шликер, полученный из кварца, полевого шпата, глины и других материалов, заливают в гипсовые формы. Чем дольше держать массу в форме, тем толще получится изделие. После того, как заготовка подсохла, ее обжигают. Это уже готовое изделие – «бисквит».Если заготовку покрыть глазурью, изделие будет называется «белье». Его можно или оставить белым и глянцевым, или расписать.
Рисунок для изделий придумывают художники. Иногда работа над рисунком длится несколько месяцев. После нанесения краски изделие снова нужно отправить на обжиг. После температурной обработки цвет рисунка меняется. Иногда, чтобы достичь нужного цвета сложного узора, фарфор подвергается обжигу по восемь раз. Если изделие нужно тиражировать, в процесс работы включаются живописцы, которые копируют рисунок на фарфоре с помощью специальных трафаретов – деколей. Прежде чем обычная фарфоровая чашка попадет на стол петербуржца, она проходит более восьмидесяти процедур.
Рисунок на некоторые изделия наносят с помощью трафарета. Фото: АиФ / Яна ХватоваИногда понаблюдать за процессом производства фарфора на завод приходят группы школьников. Дети быстро отвлекаются и начинают шуметь, но сотрудники знают, как справиться с бунтовщиками. «Когда дети начинают шуметь, мы даем им кобальтовые чашки и просим посчитать «мушечки» (маленькие точки – прим. авт.), — поделилась директор ИФЗ Татьяна Тылевич. – Они начинают считать, сбиваются, считают заново».
3d-технологии на заводе
Завод в настоящее время работает по трем основным направлениям: выполнение частных заказов, копирование знаковых экземпляров и сохранение традиций прошлых столетий. Европейские заводы давно перенесли производство в страны Азии и отказались от ручной работы. На ИФЗ старые традиции не только сохранились, но и продолжают развиваться.
«Последнее десятилетие стало началом «золотого века» завода, — уверена главный художник ИФЗ Нелли Петрова. – Мы часто проводим выставки в Петербурге и Москве, иногда даже в Италии. Я была на многих европейских предприятиях и знаю, что мы уникальны. Мы стараемся даже чашку сделать высокохудожественно».
Ко дню рождения ИФЗ на заводе открылась выставка авторских произведений художников «Яблоко». В экспозиции представлены тарелки, расписанные в теплых тонах и от этого похожие на яблоки.
Ко дню рождения ИФЗ на заводе открылась выставка авторских произведений художников «Яблоко». Фото: АиФ / Яна ХватоваПроизводство открыто для всех
Начало празднованию дня рождения завода положило торжественное богослужение у старого фрагмента мельницы во дворе завода. Мероприятие состоялось не случайно. Вот уже много лет сотрудники завода борются за восстановление церкви, которая принадлежала заводу несколько веков назад и была разрушена.
«Церковь была построена знаменитым архитектором Красовским, — рассказала Тылевич. – Мы хотим восстановить эту церковь и построить в ней фарфоровый иконостас. Получить земельный участок очень легко, но администрация города не идет нам навстречу в этом вопросе. Нас постоянно просят подождать, отложить строительство».
У завода прошло богослужение. Фото: АиФ / Яна ХватоваОднако эта проблема не мешает заводу развиваться и выпускать новые изделия. Посмотреть на процесс производства фарфора и даже самостоятельно расписать фарфоровую чашку может любой желающий. Для этого достаточно лишь позвонить на завод и записаться на экскурсию и мастер-класс.
Смотрите также:
★ Шликер — художественные техники .. Информация
Пользователи также искали:
шамотный шликер, шликер это, шликер из красной глины, шликер как сделать, шликер купить, шликер своими руками, шликерное литье, цветной шликер, Шликер, шликер, сделать, шликер это, шликерное литье, шамотный шликер, цветной шликер, шликер из красной глины, шликер как сделать, шликер своими руками, купить, руками, шликерное, литье, шамотный, цветной, красной, глины, своими, шликер купить, художественные техники.
Настоящий обжигаемый на 1240°C-1300°C фарфор.
Морские цветы. Ø 20-22 cm. В печи перед обжигом. |
Давно ни чего не писала в блоге, читатели моих статей заскучали уже наверное. Виной всему фарфор. Да-да, опять фарфор, но тот, который самый настоящий, обжигаемый в специальной печи при очень высоких температурах 1240°C-1300°C. «Горячий» 😃 фарфор из которого делают посуду, статуэтки, скульптуры, сувениры и пр.

Конечно, керамическая флористика (лепка цветов из натурального фарфора и природной глины), занятие, которое на несколько порядков усложняет задачу создания неувядающих цветов по сравнению с полимерной флористикой (лепкой цветов из полимерной глины и холодного фарфора), требует больше затрат времени, сил, настойчивости, усидчивости, но и очень радует, когда удаётся достичь успеха. Чем отличается натуральная фарфоровая керамическая масса от натуральной глины, а тем более от
холодного фарфора и полимерной глины, я напишу более подробную отдельную статью. Но уже сейчас у меня много спрашивают о том, сильно ли отличаются эти материалы, поэтому пока кратко скажу здесь: обжигаемый фарфор кардинально отличается от холодного фарфора и полимерной глины.
Фарфор в сыром виде |
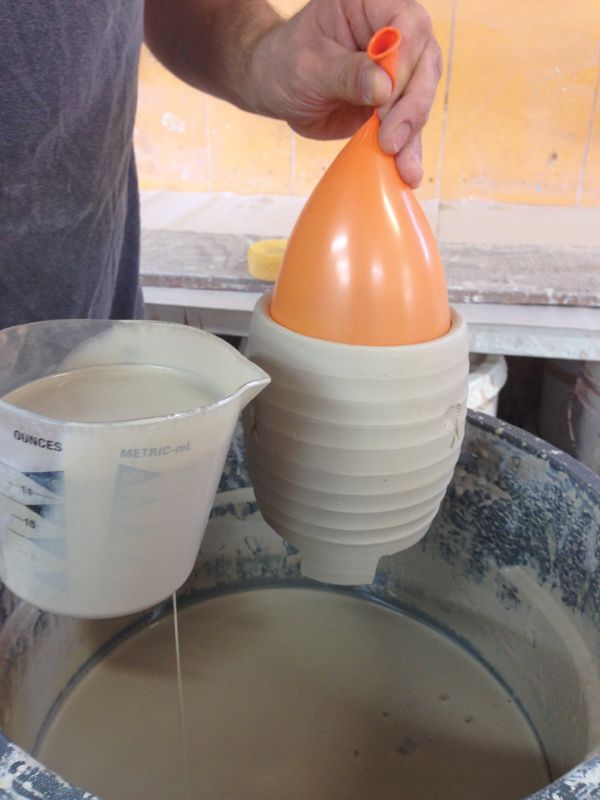
Но и в этом случае разница очень заметна, поскольку дотрагиваться до тонких высохших деталей из настоящего фарфора практически невозможно, они могут рухнуть, рассыпаться от любого неверного или неточного движения, перемещения. Он очень хрупкий и лепестки цветов могут сломаться даже от падения на них салфетки.
Но если и удалось слепить то, что задумано, надо ещё соблюдать условия сушки (влажность воздуха, не высокая температура воздуха, отсутствие сквозняков, открытых форточек и пр.) иначе изделие потрескается и рассыпется; так же надо учитывать разницу в толщине деталей и изделия, т. к. более тонкие детали сохнут быстрее и изделие тоже может треснуть и расколоться. Но и это ещё не всё — не факт, что после обжига фарфоровое изделие останется целым, не расколется, не взорвётся и не деформируется. В среднем, как говорят все мастера, 50% изделий после обжига выбрасываются испорченные.
Вот так примерно приходится сушить фарфор, придумывая всякие конструкции:
Сушка розы из обжигаемого фарфора. |
Сушка розы из обжигаемого фарфора |
Это ещё влажный, сырой фарфор:
Хризантема из фарфора |

Но даже если идеально загладить-замазать-зашкурить швы, места стыков и пр, то нет ни какой гарантии, что они останутся незаметными уже после обжига. После обжига изделие всё равно может оказаться бракованным.
Это уже высушенный фарфор, но ещё не обожжённый.
Ромашка из фарфора. |
Ромашка из фарфора. |
Учусь создавать симметричную форму на гончарном круге. Когда смотришь со стороны, как работает мастер, то кажется, что глина такая мягкая и послушная в его руках, как масло. Раз-два, и вазочка готова! … Оказывается всё на самом деле гораздо сложнее и тяжелее. Даже небольшую вазу (высотой примерно 14 см ) вот из такого маленького комочка глины без определённых физический усилий и навыков сделать совсем непросто. Я радовалась как ребёнок, когда мне удалось её просто центрировать, вытянуть в высоту и потом добиться узкой формы горлышка.
Рассчитывала написать небольшую заметку про фарфор, но про этот материал двумя словами не расскажешь…
КОСТЯНОЙ ФАРФОР | Наука и жизнь
Мне подарили изящную чашечку из костяного фарфора (изготовлена на ЛФЗ). Расскажите, пожалуйста, почему фарфор получил такое странное название и в чем секрет его производства? Наука и жизнь // Иллюстрации‹
›
И. МИЛУШКИНА (Москва).
Костяной фарфор необыкновенной белизны, тонкий и звонкий (при легком постукивании по его поверхности раздается мелодичный звук) иногда называют королевским, а еще чаще — белым золотом.
На протяжении столетий секретом изготовления фарфора владели лишь некоторые страны. Еще большей редкостью был королевский, костяной фарфор. Тончайший воздушный фарфор, известный под названием “яичная скорлупа”, был изобретен в Китае.
В Европе костяной фарфор впервые появился в Англии в XVIII веке. Английский завод Веджвуда долгие годы оставался монопольным поставщиком этого фарфора, так как особенности его производства держали в строжайшей тайне.
В России, на Ломоносовском фарфоровом заводе, костяной тонкостенный фарфор стали выпускать только в конце 1960-х годов. Но этот фарфор тоньше и белее английского! Ломоносовский фарфоровый завод — единственное в России предприятие, выпускающее подобные изделия. Костяной фарфор делают по уникальной технологии, разработанной специалистами завода, удостоенными звания лауреатов Государственной премии СССР в области науки и техники в 1980 году.
Для получения костяного фарфора в жидкую массу (шликер) наряду с глиной, каолином, полевым шпатом и кварцем добавляют предварительно обожженную костяную муку (перемолотые кости домашних животных). Именно костяная мука придает фарфору необыкновенные свойства.
После того как изделие приобретет нужную форму, его обжигают при очень высокой температуре (выше 1200оС). Затем наносят глазурь и вновь обжигают, понижая температуру на 100о. Теперь наступает очередь художников. Красоту и изящество изделиям придает изысканная роспись. Она бывает надглазурная и подглазурная.
Слой глазури на фарфоре должен быть “не толще двух бумажных листков”, — писал первый бергмейстер Императорской порцелиновой мануфактуры Дмитрий Иванович Виноградов. Первый фарфор в России называли Виноградовским, по имени его создателя. Дмитрий Иванович, трудившийся на заводе более 30 лет, оставил “Обстоятельное описание чистого порцелина, как оной в России при Санкт-Петербурге делается, купно с показанием всех тому принадлежащих работ”. Многие тонкости производства фарфора, подмеченные автором, учитываются и сейчас.
Бывший Императорский фарфоровый завод мог бы носить имя Дмитрия Ивановича Виноградова, но советские чиновники распорядились иначе, и завод стал Ломоносовским. Марка “ЛФЗ” известна во всем мире, имя Виноградова, к сожалению, знают только специалисты.
Мастер-класс «Декоративная ваза методом шликерного литья» | Материал:
Мастер-класс педагога дополнительного образования Рубаненко Д.А
«Декоративная ваза методом шликерного литья»
Место проведения: МКУДО «Дом детского творчества» г. Курчатов, Курская обл
Целевая аудитория: учителя общеобразовательных учреждений г. Курчатова и педагоги дополнительного образования
Количество участников: 10 человек.
Цель: передача коллегам личного профессионального мастерства
Задачи: — знакомство с техникой шликерного литья;
— ознакомление с особенностями шликерного литья ;
— повышение профессионального уровня педагогов;
— формирование положительного эмоционального фона, психологический отдых.
Оборудование: и доска для лепки, стеки, вода, тряпочки, стаканчики, гипсовая форма,шликерная масса, краски акриловые, кисти.
Ход занятия:
На Руси прошло длинный путь развития. В 9-10 веке люди вручную изготавливали из глины керамику. Изначально изготовлением керамической посуды занимались исключительно женщины. Чтобы глиняное тесто было крепким и вязким, к нему примешивали кусочки кварца или гранита, песок, мелкие раковины, а иногда даже осколки керамики или растения. Благодаря этому, из такого глиняного теста можно было сделать сосуды разнообразной формы.
В 9 веке на юге Руси возникло важное приспособление для работы с глиной – гончарный круг. Распространение этого новшества привело к отделению этой специальности от остального труда. Кроме того, гончарным делом теперь начинают заниматься не только женщины, но и ремесленники-мужчины. Вначале появился ручной гончарный круг. Это был простейший механизм, который управлялся одной рукой. В отверстие на деревянной скамье вставлялась ось, на которой располагался большой деревянный круг. Затем на этот круг располагали кусок глины, и, чтобы она не прилипала, заранее посыпали ее золой или песком. Сев на скамью, гончар вращал одной рукой круг, а другой формировал изделие. Немного позже появился ножной гончарный круг – механизм вращали с помощью ног. Благодаря этому, производительность труда в гончарных мастерских и качество глиняных изделий очень возросли.
В зависимости от времени и области Руси мастера изготавливали различную по форме и размерам керамическую посуду. Этот факт позволяет с большой точностью установить дату изготовления сосуда или же в каком славянском племени он был сделан. Также часто на днищах посуды ставили некое клеймо, например, какую-нибудь геометрическую фигуру, цветок или ключ. Обжиг посуды проводился в печах-горнах. Они состояли из двух уровней, на первом располагались дрова, на втором – просохшие изделия. Между уровнями находилась глиняная перегородка с проделанными отверстиями, через них горячий воздух проходил с первого уровня на второй. Внутри печи поддерживалась температура равная 1200 градусам.
Древние мастера изготавливали различную посуду: миски, сковородки, кружки, крынки, огромные горшки для зерна и другого продовольствия, горшки с толстыми стенками для приготовления пищи на огне, игрушки для детей, ритуальная посуда. В качестве украшения использовали орнамент. Очень часто он был в виде линий или волн, но также встречались и в виде кружков, зубчиков или ямочек.
Веками мастера на Руси учились гончарному делу и совершенствовали его, благодаря чему оно и достигло высокого уровня. Пожалуй, наряду с металлообработкой, гончарное дело на Руси было самым важным из ремесел.
Шликерное литье — это техника изготовления гончарных изделий путем литья в форму, без использования гончарного круга или ручной формовки. Применяется как при массовом производстве изделий из глины, фарфора и других смесей, так и при изготовлении мелкосерийных и авторских предметов.
Форма, или оправка, изготовляется из гипса. После того, как в оправку заливают шликер, она впитывает в себя воду. Глина оседает и застывает на внутренней поверхности формы, повторяя ее рельеф в малейших деталях.
Состав шликера
Основа шликера — это глина с добавками, разведенная водой. Обычно ее разводят до консистенции сметаны или густых сливок.
Шликер готовят на основе одного или нескольких видов глины, добавляя песок, шамот, электролиты и красители. Для разных видов изделий выбирают наиболее подходящий для них состав.
Технология шликерного литья
Процесс шликерного литья базируется на двух физических явлениях: способности гипса впитывать воду и способности глины отдавать воду. Возможно изготовление двух классов отливок: тонкостенные и толстостенные (полнотелые). На фоне технологий гончарного круга или ручной лепки процесс выглядит достаточно сложным. Применение его требует определенных навыков и опыта. Даже опытным мастерам обычно приходится дорабатывать отливочные формы. Весь технологический процесс от начала разработки эскиза до получения готового изделия может занять до нескольких недель.
Пример эскиза для шликерного литья
На основе эскиза можно приступать к изготовлению модели. Модель является точной копией будущего изделия, но отличается от него чуть большими размерами. Это припуск на неизбежную усушку в ходе обжига.
Модели делают из таких материалов, как пластилин, гипс, дерево, керамика или силикон. Используя модель, мастер делает разборную форму из гипса. Другие материалы, доступные в условиях мастерской, для оправки не подходят, поскольку только гипс обладает уникальным свойством всасывать воду из шликера. Форма разбирается, модель извлекается. Оправка готовится к литью. Шликер разводится и тщательно перемешивается непосредственно перед отливкой.
Собственно литейный процесс состоит из следующих этапов:
- Заливка шликера в форму
- Удаление избытков раствора
- Подсыхание отливки
- Отделение отливки от стенок формы.
После подсушивания разъедините части формы и осторожно извлеките изделие. Отливка подсушивается, при необходимости правятся недостаточно проработанные детали.
Впоследствии отливку нужно обжечь в муфельной печи, как и изделие, выполненное на гончарном круге или ручной формовкой. Изделия, выполненные методом шликерного литья, также можно покрывать глазурью. Глазурный шликер наносится на поверхность. После этого проводится повторный обжиг изделий. Компоненты глазури спекаются, образуя тонкий и гладкий стеклообразный слой.
Оборудование и материалы для литья
Для литья используется шликер определенной консистенции. На ощупь он должен быть маслянистым. В состав шликера, помимо глины и воды, включают различные добавки, меняющие консистенцию и другие свойства суспензии. В качестве добавок используют
- Другие сорта глины
- Песок
- Шамот
- Электролиты
- Красители
Важнейшим оборудованием являются формы для литья. От продуманности конструкции и качества изготовления напрямую зависит качество конечного изделия. В шликерном литье применяются гипсовые формы. Оправка обычно делается из двух частей. Для точного совмещения двух частей на одной из них предусматриваются выступы, а в другой — соответствующие им по профилю впадины. В художественном литье, отличающемся малыми сериями, части формы скрепляются резинками. Гипсовая форма для шликерного литья обладает ограниченным сроком службы, и при планировании выпуска больших партий (например, изразцов) необходимо предусмотреть изготовление нескольких оправок на каждое изделие.
Важно! Форму необходимо делать только из высококачественного скульптурного гипса. Гипс должен быть пуховым, не содержать посторонних включений и комков. Оправки, изготовленные из высококачественного гипса, способны выдерживать более сотни отливок. Если же гипс низкокачественный, то после десятка отливок стенки начинают выкрашиваться и осыпаться.
Формы, пришедшие в негодность, можно раскрошить молотком, просеять через мелкое сито и добавлять в гипсовый раствор для отливки новых оправок в пропорции не более чем 1:10.
Применение шликерного литья
Шликерное литье из глины применяется достаточно широко как в промышленности, так и в художественных промыслах.
Промышленное производство охватывает санитарную керамику, производство фигурных элементов отделки помещений, плитки и печных изразцов.
Отдельно стоит отметить производство высоковольтных изоляторов. Фарфоровые изоляторы сочетают доступную цену с отличными электрическими характеристиками, устойчивостью к перепадам температуры и отменной долговечностью. Недостатком же их является высокая хрупкость. В последнее время они стали уступать свои позиции на рынке изделиям из современных пластиков.
Этапы изготовления Декоративной вазы
1.Берём гипсовую форму и скрепляем между собой две половинки любой толстой нитью
2. Начинаем наполнять нашу форму шликерной массой (жидкая глина). Делаем это в течении часа, затем сливаем лишнюю глину обратно в ёмкость. И оставляем высыхать на 24 часа.
3. Прошли сутки мы открываем форму и достаём нашу вазу и делаем нашей вазе украшение.
4. Катаем для одного цветка ( цветков у нас будет 3шт) 6 шариков.
5.Каждый шарик надо немного раздавить и согнуть у одного края. Таким образом делаем все 18 липестков для трёх цветков.
6. Далее катаем небольшие шарики из них делаем капельки таких капелек 7штук(это листья для цветов)
7. Наши листья мы на шликерную массу в произвольном порядке клеим на вазу.
8.Начинаем собирать наши цветки, для этого каждый лепесток намазываем немного шликером и укладываем по кругу.
9. Катаем маленький шарик и приклеиваем его на шликер в серединку цветка.
10. Таким образом собираем все цветы, наносим рисунок стеком на листочки. 11.Продолжае декорировать вазу клеим на шликер небольшие колбаски .
12. Катаем небольшие шарики и тоже наносим как украшение нашей вазе.
13.Наносим рисунок стеком на шарики.
14. Наша ваза готова, теперь даём ей высохнуть в тёплом месте 2-3дня.
15. Когда наша ваза высохла мы обжигаем её в муфельной печи при температуре 850-900 градусов в течении 3х часов и вытаскиваем её из печи.
16.Расписываем нашу вазу акриловыми красками. Ваза готова.
Ну, вот мы и закончили наш мастер-класс, давайте посмотрим на работы, оценим их, что получилось лучше, что хуже, какие элементы давались труднее?
Теперь очевидно, что можем изготавливать изделия методом шликерного литья это не так ужо и трудно, важны терпение и труд, чтобы умение переросло в мастерство. Вы, как педагоги, сможете научить этому детей. Спасибо!
Как сделать отливку из глиняного тела
Готовые литейные шликеры коммерчески доступны во всех диапазонах обжига, что делает их очень удобными, но если вам интересно, как сделать литейные шликеры из обычного глиняного тела, этот пост для вас! Если вам нравится комбинировать элементы ручной сборки или метания в деталях слипка, может быть очень сложно найти литейный клин с точно такими же характеристиками усадки и поглощения, как у вашего обычного метательного или ручного тела, поэтому научиться делать литейный клин — хорошая идея. для любого гончара или скульптора.
В этом посте Paul Wandless покажет вам, как сделать форму для литья из обычного глиняного тела. — Дженнифер Поэллот Харнетти, редактор.
Обычная задача студии — свести к минимуму количество различных глиняных тел, которые у вас есть под рукой. Методы метания, ручного строительства, литья и дизайна поверхности часто требуют различных глиняных тел, чтобы соответствовать требованиям того, как создается ваша работа. Иногда глиняные тела также должны быть в разных формах, таких как обычная влажная глина, шликер или шликер.Если я вручную строю глиняный корпус с конусом 6 и хочу добавить к нему элемент для литья под давлением, мне будет сложно найти коммерческий литейный клин с конусом 6 с точно такими же характеристиками усадки и поглощения. Поэтому просто необходимо было придумать, как сделать отливку из обычного глиняного тела.
Узнайте все о покупке и использовании глиняной посуды, загрузив этот бесплатный подарок Успешных советов по покупке и использованию глиняной посуды.
Отдельная работа, сделанная из нескольких глиняных тел, может вызвать несколько проблем. Несопоставимые показатели усадки, точки созревания, содержание железа и т. Д. Могут отрицательно повлиять на конечный результат работы при использовании различных тел. По возможности всегда лучше придерживаться одного и того же тела. Мои скульптурные работы сочетают влажную глину для общего строительства и отливку для объемных элементов или для использования с различными техниками передачи изображений для обработки поверхности. Мое решение — использовать глиняное тело, с которым я работаю, и превратить его в различные типы литейных шликеров, которые мне нужны.Это гарантирует, что все детали и обработка поверхности будут одинаково усаживаться, гореть до одного и того же конуса, и все глазури одинаково воздействуют на все разные части. Самое замечательное в этом подходе — его простота. Все, что вам нужно, — это ведро на 5 галлонов, дрель с насадкой для миксера для краски, дефлокулянт и глиняный корпус, который вы хотите использовать в качестве отливки. Если вы работаете аналогичным образом, настоятельно рекомендую научиться делать слепки из глиняного тела.
Подготовка отливки
Процесс гашения глины для изготовления шликера очень прост.Шаг первый: наполните 5-галлонное ведро на 60-75% сухой глиной, а затем добавьте воды, пока она не опустится на несколько дюймов ниже края (рис. 1). Дайте настояться в течение 24 часов, затем немного перемешайте вручную палкой (рис. 2). После того, как вы перемешали смесь в течение примерно 5 минут, используйте дрель с насадкой для миксера для краски, чтобы перемешать ее до однородной массы, которая должна иметь консистенцию густого крема. Используйте палочку для перемешивания, чтобы проверить консистенцию и найти комочки глины, которые не рассыпались (рис. 3).Продолжайте перемешивать, пока не исчезнут комочки.
Измерение удельного веса
В этот момент я обычно наполняю жидкостью для кварты, чтобы использовать ее в качестве соединительной или чистящей смеси. Остальное использую для отливки шликера. Вам нужно будет измерить удельную массу шликера, чтобы определить правильное соотношение воды и глины, прежде чем дефлокулировать его с помощью жидкого силиката натрия или Дарвана. Для определения удельного веса, который представляет собой сравнение веса 100 мл воды (который составляет 100 г и, следовательно, имеет удельный вес 1) с весом 100 мл любой жидкости или шликера, с которыми вы работаете.Сначала тарируйте (обнуляйте) вес градуированной мерной емкости на весах, затем заполните ее 100 мл накладной и посмотрите, сколько она весит в граммах. Узнав вес, вы разделите его на вес эквивалентного объема воды (100 г). По сути, это сводится к перемещению десятичной точки при измерении веса влево на два места, чтобы получить удельный вес. Пример: 183 г = 1,83 удельный вес.
В целом, удельный вес от 1,80 до 1,85 обеспечивает хороший баланс текучести и прочности для большинства целей литья.Однако это число может варьироваться в зависимости от того, что именно используется. Я использовал 1,74 для объемного литья и 1,90 для плоских слябов. Различные глиняные тела имеют разные оптимальные удельные веса, которые определяются старомодным методом проб и ошибок. Удельный вес — это просто инструмент, с помощью которого вы можете отрегулировать скольжение в соответствии с потребностями вашего конкретного проекта литья. Как только вы найдете подходящее число, запишите его и используйте для глиняного тела. Если у вас удельный вес выше 1.85, и вы хотите сбить его, добавьте немного воды (только по несколько капель за раз) в свой раствор, перемешайте и повторите тест. Если удельный вес ниже 1,80, подождите 24 часа, снимите воду с верха, снова перемешайте и снова измерьте удельный вес.
Дефлокуляция клинка
Когда у вас будет правильный удельный вес, вам нужно добавить дефлокулянт в шликер, чтобы сделать его более жидким и его можно было разлить. Обычно для достижения необходимой текучести требуется всего несколько маленьких капель жидкого силиката натрия или Дарвана.Глиняные тела с высоким содержанием железа потребуют меньше дефлокулянта, чем другие. Используйте дрель, чтобы смешать дефлокулянт с шликером, и с помощью ковша или кувшина вычерпайте часть шликера, чтобы посмотреть, как он льется. Консистенция крема — это то, к чему вы стремитесь, поэтому будьте осторожны, чтобы не допустить чрезмерного дефлокуляции скольжения, что приведет к медленному неравномерному высыханию и появлению мягких пятен на готовом изделии. Просто добавляйте по несколько капель, чтобы добиться текучести, и помните, что небольшое количество дефлокулянтов имеет большое значение.
Использование того, что работает
Я проделал этот процесс с покупной глиной и с глиной домашнего изготовления.Я также добился такого же успеха при гашении глины, которая вначале была влажной, только что доставленной из мешка, или трехдневной сухой глиной. Я держу 5-галлонное ведро, чтобы бросить в него весь свой лом, и когда оно заполнится примерно на 65-75%, я превращаю его в литейный шликер. Я также просто разрезаю 25-фунтовый мешок коммерческой глины на 1-дюймовые кубики, наполняю ими пустое ведро и использую это, чтобы сделать мою форму для отливки. Мне известны разные мнения относительно начального содержания воды в глине и ее влияния на скорость водопоглощения / насыщения при гашении.По моему личному опыту, я обнаружил, что если дать глине в любом состоянии влажности погаснуть в течение 24 часов, все она прекрасно перемешается. Я предлагаю вам просто погладить глину в состоянии влажности, которое у вас обычно было в прошлом.
Чтобы узнать больше о Поле Эндрю Уэндлессе или увидеть другие изображения его работ, посетите www.studio3artcompany.com.
Вы сделали литье из глиняного тела? Поделитесь любыми дополнительными советами в комментариях ниже!
** Впервые опубликовано в 2010 г.
SlipCasting: 19 шагов (с изображениями)
Введение: SlipCasting
Это пошаговое руководство по применению скользящего литья.Скользящее литье может быть полезно для изготовления нескольких экземпляров одного объекта и для изготовления полых отливок внутри. В этом руководстве показано, как легко и эффективно отлить фарфор в уже существующую гипсовую форму. Чтобы узнать, как сделать гипсовую форму, обратитесь к руководству «Изготовление гипсовой формы» для получения дополнительной информации.
Добавить TipAsk QuestionDownload
Шаг 1: Необходимые материалы
Ниже Вы найдете изображения материалов, необходимых для выполнения этого урока. Необходимые материалы:
Гипсовая форма
Большие резинки
Бумажная или пластиковая кофейная чашка
Глиняная губка
Режущий нож для глины
Фарфоровая посуда на 1 галлон (можно приобрести в The Standard Ceramic Supply (http: // www. 7ceramic.com/)
Добавить TipAsk QuestionDownload
Шаг 2:
1. Поверните один галлон Slip посуды по горизонтали и покатайте взад и вперед в течение 5 минут, чтобы смесь хорошо перемешалась. Вы также можете встряхнуть галлон и вниз, но имейте в виду, что он будет тяжелым.
Добавить TipAsk QuestionDownload
Шаг 3:
2. Возьмите пустую пластиковую / бумажную кофейную чашку, которую вы взяли из списка материалов, и наполните ее листом из емкости объемом 1 галлон. Как только вы это сделаете, отложите пока это в сторону.
Добавить TipAsk QuestionDownload
Шаг 4:
3. Подготовьте форму, убедившись, что ее внутренняя часть чистая и сухая. Совместите две половины формы, убедившись, что отверстия совпадают. Это обеспечит герметичное закрытие и отсутствие утечек при заливке шликера.Это слепок снежного человека и тыквы, отлитый из пластиковых игрушек. Сложные формы и готовые формы также можно приобрести в отделе керамики.
Добавить TipAsk QuestionDownload
Шаг 5:
4. Когда две половинки формы соединятся вместе, скрепите их большой резинкой. Убедитесь, что они красивые и уютные. Это будет держать две половинки вместе и, кроме того, исключить утечку.
Добавить TipAsk QuestionDownload
Шаг 6:
5.После того, как вы обернули резиновую ленту вокруг формы и закрепили ее, переверните отверстие формы вверх.
Добавить TipAsk QuestionDownload
Шаг 7:
6. Возьмите кофейную чашку, наполненную жидкостью, и сожмите край чашки, чтобы получился красивый носик. Это гарантирует отсутствие утечек и плавное и красивое вытекание из стакана. Мы делаем это, потому что заливочное отверстие в наших формах не очень большое, и мы хотим уменьшить количество разливов.
Добавить TipAsk QuestionDownload
Шаг 8:
7.Медленно и аккуратно вылейте смесь в форму. Заполните форму почти до края.
Добавить TipAsk QuestionDownload
Шаг 9:
8. После того, как вы закончили заливку шликера в форму, вы должны подождать некоторое время, пока желаемая толщина не увеличится вдоль стенок вашей формы. Ниже представлена временная диаграмма, к которой вы можете обратиться для определения желаемой толщины. В то время как это происходит, вы поймете, что скольжение становится все ниже и ниже. Это происходит потому, что по мере того, как ваш шликер накапливается внутри формы, он буквально всасывает жидкий шликер в стенки формы, что приводит к снижению уровня проскальзывания.
10 минут = толщина 1/16 дюйма
15 минут = толщина 1/8 дюйма
30 минут = толщина 3/16 дюйма
40 минут = толщина 1/4 дюйма
Вы хотите оставаться в диапазоне от 15 до 20 минут для приличной толщины. Для этого урока я позволил бланку отстояться в форме на 15 минут.
Добавить TipAsk QuestionDownload
Шаг 10:
9. Вы начнете видеть слои шликера, накапливающиеся вдоль стенки формы по мере ее заполнения.
Добавить TipAsk QuestionDownload
Шаг 11:
10.Выждав 15 минут, приготовьтесь вылить излишки жидкости в кофейную чашку.
Добавить TipAsk QuestionDownload
Шаг 12:
11. Начните медленно выливать бланк из формы. Убедитесь, что вы не переворачиваете всю форму полностью, а наклоняете ее так, чтобы слиток вылился с одной стороны формы. Это обеспечивает чистоту и простоту заливки. Убедившись, что вся лишняя жидкость вылита из формы, наклоните ее на пару минут к стене, чтобы убедиться, что все капли вытекли.
Добавьте TipAsk QuestionDownload
Шаг 13:
12. Поместите отверстие формы на бумажное полотенце и дайте ему стечь в течение примерно 10 минут.
Добавить TipAsk QuestionDownload
Шаг 14:
13. Наклоните форму на бок и дайте ей высохнуть внутри формы. Подождите примерно 2 часа, прежде чем извлекать форму.
Добавить TipAsk QuestionDownload
Шаг 15:
14. После ожидания в течение 2 часов вы можете освободить форму, чтобы проверить, готова ли отлитая деталь выпасть.Вы можете определить это, посмотрев, немного ли отлитый кусок отделяется от стенок формы.
Добавить TipAsk QuestionDownload
Шаг 16:
15. Выньте отлитую деталь из формы, слегка потянув за нее. Хорошая гипсовая повязка должна позволить детали просто выпасть. Не тяните слишком сильно, это может порвать деталь. Если это доставляет вам проблемы, подождите еще несколько минут, прежде чем повторить попытку.
Добавить TipAsk QuestionDownload
Шаг 17:
16.Обрежьте нижнюю часть гипса ножом для резки глины. Этот лишний кусок всегда обрезается, поскольку он накапливается вдоль формы, где находился резервуар.
Добавить TipAsk QuestionDownload
Шаг 18:
17. Сотрите линию шва и очистите края, низ и любые другие дефекты в глиняной отливке.
Добавить TipAsk QuestionDownload
Шаг 19: Готово!
Готово! Теперь у вас есть красиво отлитый из формы фарфор.Дайте изделиям полностью высохнуть перед тем, как поместить их в печь для обжига бисквитного печенья. Для получения дополнительной информации о методах обжига в печи, пожалуйста, обратитесь к разделу «Обжиг печи»
http://lakesidepottery.com/HTML%20Text/Tips/Firing.htm
Добавить TipAsk QuestionDownload
Будьте первым, кто поделится
Вы сделали этот проект? Поделитесь с нами!
Я сделал это!Рекомендации
Создание неглазурованного керамического шликера или ангоба
Все статьи
Недорогой тестер текучести расплава глазуриОдноскоростной лабораторный или студийный смеситель для суспензии
Учебник Конус 6 Матовая глазурь с проблемами
Регулировка расширения глазури расчетным путем для устранения дрожания
Slip Alberta, 20 лет замены для Albany Slip
Обзор керамических красителей
Контролируете ли вы свой производственный процесс?
Безопасны ли ваши глазури для пищевых продуктов или они вымываются?
Нападение на стекло: механизмы коррозионного воздействия
Глазури, корпуса, ангобы для шаровых фрез
Связующие для керамических тел
Новые возможности для борьбы с увлечением: MgO (G1215U)
Керамические глазури сегодня
Номенклатура керамических материалов
Состав керамической плитки для глиняных тел
Изменение нашего взгляда на глазури
Chemistry vs.
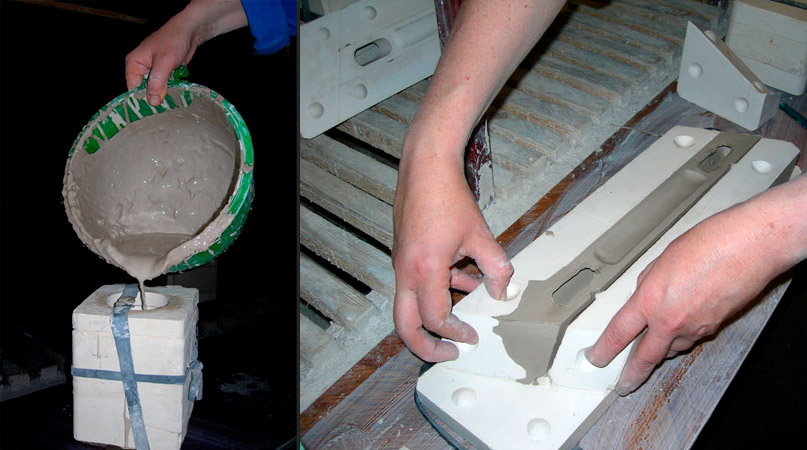
Концентрат на одной хорошей глазури
Конус 6 Рецепт плавающей голубой глазури
Медно-красные глазури
Образование трещин и бактерии: есть ли опасность?
Растрескивание в глазури для керамогранита: устранение причин, а не симптомов
Создание керамического шликера или ангоба без глазури
Создание собственной бюджетной глазури
Хрустальные глазури: понимание процесса и материалов
Дефлокулянты: подробный обзор
Демонстрация проблем, связанных с подгонкой глазури для Студенты
Диагностика проблемы отливки на заводе сантехники
Сушка керамики без трещин
Дублирование плафона Albany
Дублирование шамотного глина AP Green
Электрические печи для хобби: что нужно знать
Борьба с глазурованным драконом
Испытательные стержни из глины для обжига
Обжиг: что происходит Керамическая посуда в печи для обжига
Сначала вы это увидите, а потом уже нет: Устойчивость глазури Raku
Закрепление глазури, которая не остается в суспензии
Создание прозрачной глазури, совместимой с хромо-оловянными пятнами
Создание фарфора
Формулирование золы и естественного вещества -Материальные глазури
Формулирование собственного глиняного тела
G1214M Конус 5-7 20×5 Глянцевая базовая глазурь
G1214W Co ne 6 Transparent Base Glaze
G1214Z Cone 6 Matte Base Glaze
G1916M Cone 06-04 Base Glaze
G1947U / G2571A Cone 10 / 10R Base Matte / Glossy Glazes
Получение желаемого цвета глазури: работа с пятнами
Глазурь и пигменты для тела и Пятна в производстве керамической плитки
Основы химии глазури — формула, анализ, мол.

Химия глазури с использованием приблизительного анализа
Рецепты глазури: составьте собственное решение
Типы глазури, рецептура и применение в плиточной промышленности
Проверка вашей глазури на содержание токсичных металлов
Глянцевые глазури
Как проводится химический анализ материала
Как настольный компьютер INSIGHT справляется с единством, LOI и весом формулы
Как найти и проверить свои собственные природные глины
Как глазировать кружку лайнером
Я всегда так поступал!
Струйное декорирование керамической плитки
Расшифровка конусов Ортона
Безопасна ли обожженная посуда?
Конус выщелачивания 6 Пример использования глазури
Формулы предельных значений и целевые формулы
Низкобюджетные испытания свойств глазури в сыром и обожженном виде
Рецепт корпуса для отливки белого талька с низким уровнем возгорания
Сделайте свою собственную подставку для шаровой мельницы
Изготовление конусов для испытаний глазури
Monoporosa или Single Обожженная настенная плитка
Органическое вещество в глине: подробный обзор
Керамика, устойчивая к атмосферным воздействиям на открытом воздухе
Обзор бумажной глины
Покраска глазури вместо погружения или распыления
Распределение частиц керамического порошка по размерам
Керамогранит, керамическая плитка или гранитная плитка
Обоснование противоречивых мнений о пластичности
Ravenscrag скольжению рождается
Recylcing Scrap Clay
Снижения температуры обжига в глазури от конуса 10 до 6
одиночного огня Остекление
водорастворимых солей в минералах: Детальный обзор
некоторых ключей к работе с огневыми трещинами
Керамогранит Casting тело рецептов
Подставив Cornwall Камень
Супер-изысканный Terra Sigillata
Th e Химия, физика и производство глазури
Влияние подгонки глазури на прочность обожженной посуды
Четыре уровня, на которых следует рассматривать керамическую глазурь
Процесс изготовления керамической майолики
Физика глиняных тел
Молитва Гончара
Правильный химический состав для Cone 6 MgO Matte
Испытания на то, чтобы быть единственным техническим специалистом в клубе
Нытье останавливается: реалистичный взгляд на глиняные тела
Эти немаркированные мешки и ведра
Плитка и мозаика для гончаров
Токсичность огнеупорных кирпичей, используемых в печах
Торговля Рецепты глазури
Общие сведения о керамических материалах
Общие сведения о оксидах керамики
Сведения о свойствах глазури
Общие сведения о процессе дефлокуляции при шликерном литье
Общие сведения о рецептах шликерного литья терракотовой глазури в Северной Америке
Общие сведения о тепловом расширении в керамической глазури
Нежелательная кристаллизация в конусе 6 Глазурь
Пестрые глазури
Вулканический пепел
Wha t Определяет температуру обжига глазури?
Что такое крот, проверка крота
Что такое глазурованный дракон?
С чего начать?
Почему учебная глазурь такая сложная
Описание
Иногда бывает трудно найти ангоб, который при сушке и обжиге совместим с вашим телом. Лучше понять, сформулировать и настроить собственный промах под собственное тело, глазурь и процесс.
Артикул
.Неглазурные пластины (называемые ангобами при нанесении толстым слоем) для украшения керамики и плитки издавна вызывали большой интерес. Практически все восхищались простой красотой терракотовой посуды, декорированной белой накладкой и обработанной прозрачной глазурью. Многие гончары применяют этот старинный процесс для изготовления керамических изделий и фарфора. Промышленность, особенно плитка, обычно применяет блинчики и ангобы (например.грамм. белые слои наносятся на более темную сухую плитку перед нанесением глазури). Они почти повсеместно используются в процессе одиночного пожара. Это логично, поскольку их основное применение — прикрытие темных горящих или грязных тел, сделанных из местных материалов, в таких ситуациях с разумной стоимостью не имеет смысла стрелять больше, чем необходимо.
Сочетание пластинок толщиной с ангоб и определенного тела сложно, поэтому рецепты распространяются даже хуже, чем глазури. Они должны быть совместимы с сушкой, обжигом и тепловым расширением как с основным телом, так и с вышележащей глазурью.Каждый из них следует проверять индивидуально. Сравните это с нанесением глазури непосредственно на бисквит: вам нужно только сосредоточиться на совместимости теплового расширения с телом; это намного проще.
Рассмотрим первую серьезную проблему: адгезию к телу (как при сушке, так и при обжиге), чтобы материал прилипал! Если шликер нанесен достаточно толстым и не усаживается с нужной скоростью или количеством во время сушки и обжига, то разовьются трещины или он отслоится. Независимо от того, какая логика, теория или лабораторные инструменты могут указывать или что другие могут посоветовать, если происходит растрескивание или отслаивание, гораздо более вероятно, что вам нужно отреагировать, изменив рецепт надлежащим образом, чем изменив способ его приготовления или применения.В достижении совместимости при обжиге и сушке задействованы различные факторы, и изменение, улучшающее один аспект пригодности, может отрицательно повлиять на другой. Хотя каждый материал в рецепте используется для сушки, обжига, адгезии, теплового расширения или по эстетическим причинам, он также потенциально вреден для одной или нескольких других частей процесса; это означает, что разработка правильного рецепта — это настоящее жонглирование.
Наиболее очевидное применение мелкозернистого белого ангоба — это покрытие темного (и, возможно, крупнозернистого) тела, так что ярко окрашенная или слегка затененная глазурь появляется, как на тонком фарфоре.Производство плитки на сегодняшний день является крупнейшим потребителем ангобов, для них очень часто используются красные горящие глины (они часто доступны на местном уровне и при низких температурах горят намного сильнее, чем легкие горящие глины). Они покрывают красные тела белым горящим непрозрачным ангобом. Очевидно, что хорошая адгезия к обожженному телу имеет первостепенное значение, поэтому ангобу требуется фритта или другие плавильные машины для создания стеклянной связи. Очевидно, что адгезия будет лучше всего на стекловидных телах, где может развиться граница раздела (если тело не будет хорошо стекловидаться, потребуется дополнительная фритта, чтобы создать более гладкую поверхность раздела, но не настолько, чтобы терялась непрозрачность).
Сухая адгезия, усадка, твердость; Суспензия пульпы
- Неглазурные шликеры обладают физическими рабочими свойствами, которые определяют, насколько хорошо они окрашиваются, окунаются или распыляются; насколько хорошо они прилипают, как они стекают после погружения, как быстро они высыхают, чтобы достичь того же содержания воды, что и нижележащая твердая кожа (если наносится на этом этапе), какой толщины их можно наносить с каждым слоем, могут ли двойные слои насколько хорошо они остаются в суспензии во время хранения, насколько они склонны к гелеобразованию и т. д.
- Казалось бы логичным, что поверхность тела нуждается в некоторой шероховатости, чтобы дать скольжению место, за которое можно зацепиться. Это верно для нанесения глазури на бисквитную посуду, но не для скольжения по сухому телу. Но скольжение влажное, и любые существующие неровности на сухой поверхности тела в любом случае будут сглажены влажностью. Скольжение и тело — это глины, они липкие и поэтому имеют естественное сходство друг с другом.
- И глазури, и шликеры дают усадку во время высыхания, поскольку содержат глину.Хотя шликеры наносятся тонко и склеивание обычно не является проблемой, сушка и склеивание ангобов намного сложнее. Они гораздо менее похожи на глазурь (и более похожи на глину), поэтому казалось бы, что будет больше проблем с растрескиванием во время высыхания (из-за усадки). Однако на практике это не обязательно. Ангобы даже с 10% -ным содержанием бентонита (чего вы никогда не увидите в глиняном корпусе) часто хорошо подходят как для твердой кожи, так и для сухой посуды. Дополнительная липкость, кажется, является ключом к этому явлению.Очевидно, что один и тот же промах не будет хорошо держаться во всех ситуациях, вы должны определить рецептуру, а также когда и как ее применять. Например, если в ангобах не хватает пластиковых ингредиентов, они отслаиваются при сушке.
- Если он наносится на этапе твердости кожи и имеет значительную толщину, то скольжение должно высохнуть до того же содержания воды, что и тело, а затем сжаться вместе с телом, очевидно, что окончательный период усадки покажет разницу между ними.
(если вы собираетесь нанести глазурь на сухой скользящий слой, который снова намочит и проверит соединение).Совместимость при сушке можно проверить простым наблюдением: легко отличить пластинки с такой оболочкой, потому что они недостаточно усаживаются (при нанесении на твердую кожу), или трескаются, потому что они слишком пластичны и слишком сильно сжимаются.
- Хотя наносить покрытия толщиной ангоба на сухую посуду непрактично, часто их можно наносить тонким слоем (кистью) без особых проблем. По нашему опыту, даже шликер с 45% каолина и 10% бентонита не трескается при нанесении на сухую посуду.Фактически, шламы без бентонита отслаиваются. Кажется, что липкость скольжения важна. Очевидно, при наблюдении вы увидите, трескается он или отслаивается, и при необходимости отрегулируйте. Каолины меньше всего усаживаются, шарики — гораздо больше. Каолины доступны во многих конечных размерах частиц, чем больше размер, тем меньше будет усадка (и тем менее твердой будет сухая глазурь).
Можно использовать органические связующие для придания или улучшения свойств твердения и сцепления, но их выгорание может вызвать проблемы во время обжига (с прилипанием к скольжению и несовершенствами глазури).
- Скольжение не предотвратит отложение растворимых солей (из организма), они просто мигрируют через него и останутся на его поверхности, поскольку вода испаряется и оставляет их. Таким образом, для их осаждения в организме требуется достаточное количество карбоната бария.
Усадка и прилипание в огне
Граница раздела между шликером и телом в обжиге никогда не будет такой хорошей, как между глазурью и телом. Это потенциально является слабым местом, если сцепление скольжения не оценивается и не оптимизируется.Поскольку шликеры не плавятся, рецептура обычно делается на уровне рецепта (физические свойства должны просто соблюдаться, керамические расчеты в действительности не применимы).
- Обожженный слой скольжения может быть неплотно или плотно связан с нижележащим телом.
Шликер, содержащий стекловидные флюсы, которые плавятся и текут, образует поверхность раздела со стекловидным телом, чтобы надежно удерживать его (тело также может поставлять некоторые стекловидные флюсы, чтобы сформировать лучшую поверхность раздела с покровным стеклом). Если тело не стекловидное, то даже стекловолокно толщиной ангоба может отсоединиться, просто взяв с собой часть поверхности тела.Если шликер не стеклянный, его можно только механически прикрепить к имеющимся неровностям поверхности. Таким образом, очень важно убедиться, что шликер имеет такую же усадку в огне, что и тело (даже небольшие отличия могут нарушить сцепление).
- Ангоб слишком стекловидный, он может треснуть и в некоторых местах оторваться от тела. Как? Для глазурей с высоким содержанием глины нормальным является образование трещин при повышении температуры в печи, это побочный продукт усадки, связанной с плавлением на ранней стадии и уплотнением керамического порошка.Однако по мере того, как глазурь тает, трещины снова заживают.
Но с ангобом жидкая фаза заживления никогда не наступает. Таким образом, существует натянутый канат, по которому можно пройти между ангобом, который достаточно стекловидный, чтобы образовать связь, но не настолько стекловидный, чтобы страдать от усадки расплава на ранней стадии.
- Существует разница между целостностью связи, когда плитка выходит из печи, и в течение длительного срока ее полезного использования. Если ангоб и корпус не усадятся вместе, возникнет напряжение, если печь не обнаружит этого, может быть выполнено простое испытание на скалывание.Способность толсто нанесенного шликера удерживаться во время обжига, а также выдерживать испытания на механическую стружку, является еще лучшим тестом на совместимость с усадкой при обжиге.
- Ангоб, как и тело, имеет характерную усадку при обжиге. Они должны сжиматься вместе во время охлаждения в печи таким образом, чтобы не создавать напряжения, которое может ослабить связь скользящего тела. Не только общая усадка должна совпадать, но и кривые усадки должны быть аналогичными.
Напрягите связь, чтобы проверить и определить, является ли связь проблемой в первую очередь.Если нет, то это несоответствие усадки, отрегулируйте в правильном направлении и повторите попытку.
- Усадку ангоба в огне можно увеличить, используя большее количество флюсов для усиления стеклования или плавления, или используя глину с более мелкими частицами. Во многих случаях практично сделать образец шликера и сделать испытательные стержни для измерения усадки в огне, это отличный способ количественно оценить эффекты сушки и обжига при изменении рецептуры.
Тепловое расширение
- Для совместной работы в качестве обжигаемого объекта тело и скольжение должны иметь одинаковое тепловое расширение.Если покровный слой на керамическом изделии относительно тонкий, обычно проблем не возникает, но как только он наносится достаточно толстым, чтобы функционировать как ангоб, его следует рассматривать как отдельный объект, который имеет свой собственный коэффициент теплового расширения.
Если во время использования объект нагревается или охлаждается быстро, величина расширения и сжатия должна быть одинаковой для скольжения и тела. Если существует достаточная несовместимость, соединение ангоба с телом станет точкой разрушения, и оно может отслаиваться в уязвимых местах (например, на краях и ободах).
- Когда глазурь наносится на эго или скольжение, возникают большие сложности. Шликер действует как буферный слой, и он должен быть совместим с расширением как с нижележащим телом, так и с вышележащей глазурью. Как? «Совместимость» по тепловому расширению для шликера отличается от шликера, шликер не может подвергаться одинаковому сжатию, потому что он гораздо менее тесно связан с нижележащим телом. По той же причине вышележащие глазури не должны слишком сильно сжимать шликер, иначе они могут нарушить его сцепление с телом.Глазури, возможно, должны иметь меньшее расширение, чем при нанесении непосредственно на тело. Сложность подбора накладок для изготовления функциональной посуды, способной выдержать постоянное нагревание и охлаждение, может быть очень обременительной (для сравнения, напольная плитка испытывает лишь умеренные колебания температуры во время службы).
- Вы можете проверить вероятность сохраняющейся целостности соединения скользящего тела в связи с тепловым расширением: тест IWCT (который нагружает его путем внезапного охлаждения поверхности) и тест BWIW (внезапное расширение при погружении в горячую воду демонстрирует не подвергается ли ангоб слишком сильному сжатию).
Форма и заявка
Чтобы добиться успеха с ангобами, вам нужно другое мышление, чем в случае с глазурью. Глазури сглаживаются при плавлении, ангобы — нет.Как и краска, поверхность, которую вы наносите, получается после обжига. Таким образом будут видны потеки, вариации толщины, шероховатости, точечные отверстия, пузыри и т. Д. Обычно верхний слой глазури не может быть достаточно толстым, чтобы покрыть проблемы при укладке шликера, фактически, неровности проскальзывания могут привести к дефектам глазури. Укладывать плитку просто, так как поверхность ровная и горизонтальная, но для неровных форм это намного сложнее. Вот несколько идей.
- Рассмотрим шаровую фрезеровку
- Для хорошего нанесения необходимо произвести флокуляцию.Обычно это означает, что им нужно достаточно воды, чтобы они хорошо текли, а затем добавление флокулянта, чтобы они оставались на посуде, не двигаясь после нанесения.
- Наклейки должны быть без пузырьков, чтобы наносить их на безупречную поверхность. Пузыри могут образовываться по мере того, как они оседают с течением времени (например, они могут быть продуктом разложения частиц материала). Смешивайте с помощью миксера с регулируемой скоростью, чтобы он всасывал водоворот, но не всасывал воздух в смесь. Если скорость правильная, существующие пузырьки лопнут на поверхности, когда они будут рядом, и у вас будет шелковистый гладкий продукт, с которым можно работать.
- Шлифовки более непрозрачны, чем глазури, и теоретически обладают лучшей «укрывистостью», позволяющей им покрывать тело и маскировать его цвет и характер поверхности (включая сглаживание шероховатой или грубой поверхности, затемнение нежелательного цвета, скрытие пятен и дефектов поверхности ( например, вызванные примесями железа), уплотняя и герметизируя пористую и мягкую поверхность и обеспечивая более белую поверхность, чтобы сделать цвета глазури ярче).
Однако на практике слишком тонкие клинья могут иметь удивительно небольшую укрывистость.
- Опрыскивание может работать хорошо, но вам понадобится распылитель, который сможет работать с опрыскивателем с минимально возможным содержанием воды. Устройства с гравитационной подачей хороши (банка над соплом). Однако, если шликер слишком вязкий, он осядет в виде капель и даст неровную поверхность. Может помочь более высокое давление воздуха, но при этом образуется больше распыляемого и дышащего тумана, а поверхность покрывается галькой. Достаточно толстый слой укладки, скрывающий недостатки тела, может оказаться проблемой.С одной стороны, на нанесение нескольких слоев требуется дополнительное время, в то время как попытка распыления толстого единого слоя может привести к образованию капель и хрупкого предмета, забитого водой, не говоря уже о скольжении, которое может потрескаться и оторваться при высыхании. Вы можете обнаружить, что нагревание посуды (при условии, что вы распыляете насухо (посуда без бисквитного покрытия) поможет высушить скольжение и позволит вам нанести более толстый, ровный и гладкий слой.
Как и в случае с глазурью, лучше всего иметь процесс, при котором стекло сохнет быстро
- Заливка слипа может очень хорошо подойти для некоторых форм (например.грамм. непрерывное применение водопадного типа). Но это может быть практично только для нанесения одного слоя: ваша консистенция скольжения, температура посуды, способ нанесения — все должно быть правильным, чтобы избежать подтеков и перекрытия слоев.
- Погружение не совсем практично для нанесения ангоба на высушенную посуду. В то время как окунание обожженного бисквитного предмета с помощью щипцов — это простая процедура, которая очень хорошо работает, для сухого предмета это непрактично, потому что предметы не обладают достаточной прочностью, чтобы удерживаться щипцами, и даже если они это сделали, вода из клинка вызовет объект рассыпаться от стресса, связанного с прикосновением.Раньше таким способом делали тяжелый керамогранит, он имел достаточную толщину, чтобы выдержать обращение. Однако в наши дни никто не может позволить себе обстреливать тяжелые предметы (а требования к качеству выше).
Однако изделия из жесткой кожи можно окунать в ангоб. Это может сработать очень хорошо, однако ангоб снова намочит всю деталь (если стенки тоньше), и для придания жесткости может потребоваться много часов.
- Слои скользящей толщины можно наносить кистью на различных этапах процесса.Однако с этим есть проблемы. Тонкостенные изделия из кожи и изделий из кожи станут мягкими и податливыми до такой степени, что с ними нельзя будет обращаться (несколько слоев могут потребовать длительного времени для застывания между ними). Мазки кистью часто будут хорошо видны (хотя иногда это необходимо). Пористый бисквит быстро сушит мазки, иногда настолько быстро, что кисть прилипает (что делает невозможным покрытие). Чтобы избежать этой проблемы, печенье можно обжечь и выше, но более высокая плотность может означать медленное высыхание. Даже в этом случае бывает трудно добиться равного покрытия.Использование жевательной резинки — это способ очень хорошо наносить скользящую краску на бисквитной посуде (см.
Ссылку «Глазури для нанесения кистью» ниже).
Рецепт
Концептуально рецепт может быть таким же простым, как фарфоровый корпус с достаточным количеством добавленной фритты для прилипания, но не настолько, чтобы проявление стекла уменьшало непрозрачность. Это может быть тонкая грань. Например, только 15% ферро-фритты 3134 может слишком сильно расплавить его в конусе 04. Лучше смешать ингредиенты, содержащие ингредиенты для фарфора, вместо того, чтобы просто добавлять что-то в порошкообразный фарфор, рецепт которого вы не знаете. знайте, это даст вам необходимую гибкость для настройки.
При высоких температурах вы должны иметь возможность флюсовать, используя полевой шпат и другое сырье, а не фритты (например, волластонит, доломит). Таким образом, переделкой стандартного фарфора 25 может быть 40% каолина, 35% полевого шпата, 25% кремнезема (я объединил шариковую глину и каолин только в каолин (для дополнительной белизны), вам может потребоваться добавить пластификатор, например Veegum. Если он может быть более зрелым, попробуйте на этот раз полевой шпат 40. Для средней температуры типичный рецепт основного фарфора может включать 40 каолина на шарик глины, 40 полевого шпата и 20 кремнезема.Добавьте 5% борной фритты (например, Ferro 3134). Идея состоит в том, чтобы настроить его степень зрелости, чтобы добиться максимального плавления без потери непрозрачности.
Для большей белизны рассмотрите возможность использования более белого каолина или добавления некоторого количества циркопакса (возможно, 5% для непрозрачности). Если шликер слишком пластичный, используйте кальцинированный каолин в качестве части глиняного дополнения, если это необходимо, чтобы уменьшить усадку при высыхании. Если он отслаивается, попробуйте добавить Veegum (до 10%). И в крайнем случае используйте жевательную резинку, чтобы она затвердела и улучшила текучесть (однако, лучше отрегулировать или заменить глину, чтобы получить необходимые свойства текучести и высыхания, смолистые шликеры сохнут медленнее).
Несколько общих замечаний по использованию Slip
- Дополнительным тестом на сцепление с телом ангоба является простое разрушение обожженного предмета на мелкие кусочки и тщательный осмотр осколков, чтобы увидеть, преобладают ли линии излома на границе раздела скользящего тела.
- В то время как слипы могут действовать как среда для пятен и красок из оксидов металлов, пятна не приобретают свой цвет также в слипах (из-за отсутствия стекловидной фазы и непрозрачности слипсов единственными частицами пятен, которые влияют на цвет, являются те, которые экспонируются поверхность).Как и в случае глазури, смесь должна иметь химический состав, совместимый с системой окраски (у каждой отдельной системы окраски есть свои потребности, и может потребоваться настройка смеси для конкретных систем). Рецепт может даже потребовать корректировки различных пропорций определенных цветов (например, огнеупорных) для поддержания той же степени развития расплава.
- Разбери свой ангоб.
Например, с такой проблемой, как отслаивание, мы, как пользователи, должны признать, что ангобы плохо прилипают в лучшие времена.И мы отвечаем за рецепт. В нашей формулировке и процессе мы можем сделать так много вещей, чтобы заставить их потерпеть неудачу и сделать их устойчивыми к неудачам. Еще важнее то, что мы обязаны понять механизмы процесса ангобирования, связанные с нашим рецептом. Если шелушится, почему? Мы контролируем его усадку и пластичность, например, чтобы иметь возможность распознавать различия. Лучше спросить поставщика: «Почему у вашей глины теперь усадка при высыхании 7%, когда она составляла 5%?», Чем говорить «ваша глина — причина того, что мой ангоб не работает».Мы все еще можем быть причиной того, что это не работает, даже если их материал немного изменился. Наши рецептуры должны быть терпимыми к некоторым изменениям в материале, а не должны быть сформулированы так, чтобы быть на грани «проблемной пропасти».
Создание вашего собственного бланка потребует времени, решимости и методичного подхода с большим количеством адаптации с течением времени. Как и в случае с глазурью, гораздо лучше иметь один рецепт, который вы понимаете и контролируете, чем возиться с 10, которые вы не понимаете и которые не работают?
Связанная информация
Создание равновесия тело / скольжение в терракотовой посуде
L3685X white slip (левая кружка) содержит на 5% больше фритты, чем Y (правая).Фритта плавится, образуя больше стекловолоконных связей, чтобы прикрепить ее к телу (она также твердеет и немного затемняет цвет). Но фритта также увеличивает усадку при обжиге, «растягивая» белый слой на теле по мере остывания печи (это демонстрирует слегка изогнутый брусок из биглины). Однако глазурь G2931G подвергается некоторому сжатию (для предотвращения растрескивания), поэтому она «отталкивается» от белого покрытия. Это создает состояние равновесия. Скольжение Y справа находится за пределами равновесия, оно отслаивается по краю, потому что сцепление недостаточно хорошее.Добавление большего количества фритты, другой стороны баланса, приведет к чрезмерному натяжению скольжения, уменьшению прочности изделий и увеличению разрушения при воздействии теплового удара (сильно скрученный биглиновый стержень спереди, а не эта глина / скольжение демонстрирует натяжение плохо подогнанная комбинация могла наложить).
Тот же ангоб. Такое же содержание воды. В чем разница?
Ангоб слева, несмотря на то, что он имеет довольно низкое содержание воды, стекает с кожаной твердой глины, капая и медленно высыхая.Тот, что справа, был флокулирован солями Эпсома (в порошке), что придает ему тиксотропность (способность образовывать гель, когда он не в движении, но течет во время движения). Теперь нет подтеков, нет тонких или толстых участков. Через несколько секунд он загустеет, и его можно поставить вертикально на полку для сушки.
Из-за добавления воды этот белый ангоб действительно меньше растекается? Как?
Белая накладка (нанесенная на жесткую кожаную чашку) слева стекает вниз с обода (даже если ее держали вверх дном в течение нескольких минут!).Тем не менее, эта суспензия была очень вязкой с удельным весом 1,48. Почему? Потому что он не был тиксотропным. Исправление? Я разбавил его до 1,46 (чтобы он стал жидким) и добавил щепотки порошкообразной соли эпсома (при энергичном перемешивании), пока он не загустеет достаточно, чтобы остановить движение примерно через 1-2 секунды после выключения миксера. Но за этой остановкой следует отскок. Это тиксотропия. Легко переусердствовать с солью Эпсома (слишком сильно загустевать), я добавляю пару капель Дарвана, чтобы разбавить его, если нужно. Когда ангоб станет правильным, он загустеет примерно через 10 секунд сидения, поэтому я могу перемешать его, окунуть и извлечь кружку, встряхнуть, чтобы слить, а затем он загустеет и удерживается на месте.Имейте в виду, что это гончарный проект. В промышленности ангобы дефлокулируют, чтобы снизить содержание воды. Но дефлокулированный шлам все же может загустевать (если он жидкий).
Решение сложной проблемы отслаивания ангоба
Это демонстрирует трудности, с которыми вы можете столкнуться, пытаясь заставить ангоб работать с глиняным телом. Здесь проскальзывание / глазурь отслаивается от края кусков на конусе 04 (не происходит на 06). На передней биглиновой планке видно, что белая и красная глины хорошо сохнут вместе (при высыхании образовалась небольшая кривая).Вместе они тоже хорошо стреляют (кривизна при стрельбе не менялась). Два задних тонких стержня, кажется, демонстрируют совместимость с тепловым расширением: толстый слой глазури не подвергается достаточному сжатию, чтобы искривить любой стержень во время обжига. В то время как белая глина содержит 15% фритты и образует хорошую связь с красной массой, эта связь не так хороша, как связь между глазурью и белой глиной. Тем не менее, он все еще отслаивается от обода на стыке скольжения и корпуса. Почему? Сначала казалось, что при инверсии кварца происходит сбой (потому что в теле кварца меньше, чем в белом шликере).Однако теперь оказалось, что комбинации сжатия шликера и глазури достаточно, чтобы разорвать связь шликера с телом на выпуклых контурах. Сжатие шликера и глазури, вероятно, плохо проявилось на брусках, потому что при такой низкой температуре они недостаточно стекловидные, чтобы их легко скручивать.
Полоски из би-глины для проверки совместимости ангоба с телом
Слипоны и ангобы надежны, верно? Просто смешайте рецепт, который вы нашли в Интернете или который рекомендует кто-то другой, и готово. Неправильный! Накладки с низким уровнем пламени должны быть совместимы с телом по двум принципам: сушка и обжиг. Терракотовые тела имеют низкую усадку на конусе 06-04 (но высокую на конусе 02). Процентное содержание фритты в ангобе определяет его усадку при обжиге при каждой из этих температур. Слишком много — ангоб растягивается, слишком мало — сжат. Чем ниже фритта, тем меньше прилипание стекла к корпусу и больше вероятность отслаивания, если стекло хорошо подогнано (либо во время обжига, либо после того, как покупатель подвергнет ваш продукт нагрузке).Ангоб также должен давать усадку вместе с телом во время высыхания. Как можно измерить совместимость? Боди-полоски. Сначала я готовлю пластиковый образец ангоба. Затем я скатываю плиты толщиной 4 мм и туловище, кладу их лицом к лицу и снова скатываю до 4 мм. Я режу бруски размером 2,5х12 см, сушу и обжигаю. Скручивание указывает на несоответствие. Этому ангобу нужно больше пластичной глины (чтобы он давал больше усадки при высыхании) и меньше фритты (чтобы меньше усадка при обжиге).
Слишком много фритты в ангобе — он потеряет непрозрачность и белизну
Белая накладка слева — это приспособление к популярной накладке для рыбного соуса (L3685A: 8% Frit 3110 заменяет 8% Pyrax, чтобы сделать его более твердым и лучше прилегать к телу).Тот, что справа (L3685C с 15% фритты) становится полупрозрачным, очевидно, он будет иметь более высокую усадку при обжиге, чем тело (частая причина дрожи на губах и изменений контура). Слип представляет собой очень пластиковый белый корпус. Поскольку при слабом огне они не такие стекловидные, как красные, они нуждаются в помощи, чтобы созреть, и фритта — естественный ответ. При правильном количестве усадка корпуса и шликера может быть согласована, и шликер будет непрозрачным. Это подчеркивает необходимость настраивать зрелость ангоба в зависимости от тела и температуры.Хотя циркон можно было добавить к циркону справа, чтобы сделать его непрозрачным и побелить, это не устранило бы несоответствие в усадке в огне между ним и телом.
Крайний случай несоответствия усадки при обжиге ангоба и корпуса
Пример обожженного белого ангоба до конуса 2. Во время обжига он сжался, и сцепление с корпусом было полностью нарушено. У корпуса есть усадка при обжиге около 6%, но скольжение ближе к 10%. Поскольку глазури плавятся, они не имеют усадки при обжиге.Но ангобы есть, и они должны быть совместимы с телом.
Нанесение ангоба путем заливки или распыления
Пример ангоба (шликера), нанесенного на сухую посуду и затем обстрелянного по конусу 2. Один левый залит, правый распылен. Контроль толщины ангобов важен, поэтому очень важны удельный вес и вязкость суспензий. Ангобы бесценны, так как красное или коричневое горящее тело можно заставить гореть белым, как фарфор (что обеспечивает гораздо лучшее качество поверхности глазури).
Ссылки
Материалы | Скольжение вороньих скал |
---|---|
Глоссарий | Глазурь для мокко Техника, используемая художниками-керамистами для украшения керамики. ![]() |
Глоссарий | После огневого остекления Относится к практике обжига керамики за один обжиг (а не за два) для получения полностью глазурованного продукта.Эта практика требует больше технических знаний. |
Глоссарий | Керамический шликер Термин Slip может иметь различные значения в традиционной керамике. |
Глоссарий | Чистящая глазурь Любители и все большее число гончаров используют коммерческие глазури для рисования. Удобно, много визуальных эффектов. Но есть также проблемы по сравнению с созданием собственного. |
Проблемы | Ползание глазури Задайте себе правильные вопросы, чтобы выяснить настоящую причину ползания глазури.Решайте проблему, а не симптомы. ![]() |
Статьи | Рождение Вороньего Утеса История открытия и разработки Ravenscrag Slip может помочь вам распознать потенциал глины, к которой у вас есть доступ. |
Тони Хансен
Авторские права 2008, 2015, 2017 https://digitalfire.com, Все права защищены
Простое пошаговое руководство по шликерному литью
Шлифовальное литье для меня всегда было одним из самых сложных художественных процессов, которые нужно выполнить.Путем многих проб и ошибок с моими учениками я наконец нашел процесс, который работает в моем классе. Я хотел бы поделиться этим с вами сегодня, чтобы вы, возможно, захотели присоединиться к своим ученикам.
Я считаю, что цельная форма конической чашки — самый простой способ начать. В идеале это должна быть чашка, которую ученик бросил на колесо или даже сделанная вручную. Однако, если вы просто экспериментируете или впервые пытаетесь выполнить скользящее литье, возможно, вы даже захотите купить дешевую чашку в долларовом магазине. То, что я вам здесь показываю, возможно, не является самым технически чистым или правильным методом, но это то, что работает в моем классе. Ниже представлен наш процесс.
Процесс изготовления форм
1. Купите себе ящик, в который можно налить гипс. Коробка из-под обуви, полгаллона молока или сока, что угодно. Мне нравится картон, потому что он довольно легко отделяется от гипсовой формы.
2. Поместите небольшой слой глины на дно коробки, плоский и ровный.Это будет удерживать чашку на месте, пока вы перевернете ее внутрь контейнера. Вы можете попробовать это без глины, но я обнаружил, что иногда чашка всплывает на поверхность гипса и портит весь процесс.
Дополнительно: Вы можете покрыть чашку вазелином или силиконовым спреем, чтобы гипс не прилипал к чашке. У меня не было проблем с этим, но лучше перестраховаться, не так ли?
3. Перемешайте гипс (подойдет любой тип) и после того, как он полностью перемешается, вылейте его в коробку. Старайтесь наливать в сторону коробки, а не прямо в чашку.
4. После того, как штукатурка затвердеет — я обычно жду 24 часа — вы можете оторвать коробку от формы и удалить чашку. Вы готовы к промаху!
Процесс скользящего литья
1. Для начала убедитесь, что ваш слип жидкий и легко разливаемый. Если вы используете новый слип, он должен быть готов к работе. Если вы перерабатываете слип, я предпочитаю использовать блендер и немного воды, чтобы добиться необходимой консистенции.
2. Медленно вылейте шликер в форму, пока он не достигнет самого верха. Оставьте форму полной примерно на 15 минут, чтобы внешняя часть чашки застыла. (Время можно изменить позже, если вы обнаружите, что готовый продукт слишком толстый или слишком тонкий.)
3. Затем вы можете вылить остаток отливки обратно в стакан, и этот слип можно повторно использовать для другой стакана, если он останется чистым.
4. Когда чашка станет твердой кожей, она начнет отделяться от формы. Тогда вы знаете, что снимать безопасно и достаточно прочно, чтобы с ним можно было обращаться.
5. Вы можете использовать нож X-Acto или зеленую мочалку, чтобы выровнять верхний край и убрать все дефекты. Вы можете вырезать узоры или просто оставить все как есть, чтобы внешний вид получился гладким. После этого все должно быть готово к обжигу бисквитного печенья!
Эта монолитная форма представляет собой наиболее простую форму изготовления форм.Это может быть намного сложнее, если используются формы из двух и трех (или даже больше!) Частей. . . но это кое-что для другой статьи в другой день. Пока придерживайтесь простого процесса, а когда вы почувствуете себя более амбициозным и будете готовы к созданию формы из двух частей, отправьте мне электронное письмо. Буду рад помочь!
Пробовали ли вы когда-нибудь скользящее литье в своем классе? Как прошло?
О каких проблемах (или решениях) вы бы хотели предупредить или рассказать?
Что еще вы хотели бы знать?
Как скользить литье керамики
Шликерное литье облегчает массовое производство керамики, но не требует особого специального оборудования и может выполняться в мастерской. В зависимости от того, сколько у вас форм, с помощью скользящего литья можно создавать сотни идентичных деталей. Некоторые гончары склонны отдавать предпочтение этому методу, поскольку скользящее литье значительно упрощает изготовление деталей, которые сложно вручную собрать или создать на круге. Еще одно замечательное преимущество скользящего литья состоит в том, что вы можете изготавливать такие изделия, как кувшин с ручкой, как одно целое. Скользящее литье также является отличным методом для создания более сложных предметов, таких как чайник.
Шликер — это просто жидкая смесь глины или «жидкая суспензия частиц глины в воде», которая обычно немного тоньше суспензии.Шликер — это «жидкая глина, залитая в гипсовую форму». Соотношение примерно 75 процентов глинистого тела к 25 процентам воды.
Как превратить ваше глиняное тело в скольжение
Процесс превращения вашей глины в шликер называется процессом гашения. Важно использовать глину одного и того же типа, чтобы ее можно было обжигать при одинаковой температуре. Разбавьте необходимое количество глины и воды и добавьте их в большое ведро, чтобы они гасили (распадались).У разных глин разное время гашения, но вы должны оставить глина растворяться в воде примерно на 24 часа. Для этого глина должна быть сухой. По истечении этого времени смесь нужно будет аккуратно перемешать большой палочкой. Чтобы получить идеальную консистенцию (ваш лоскут должен быть толщиной со сливки), вам понадобится дрель с насадкой для смешивания, чтобы сделать лоскут гладким. Важно определить, имеет ли шликер правильное соотношение глины и воды (известное как его удельный вес).Чтобы измерить удельный вес, вам нужно налить 100 мл глиняной смеси в мерный кувшин и взвесить ее в граммах. Затем разделите полученный вес на 100 (или количество миллилитров, которые вы вылили), и это число будет вашим удельным весом. Хорошее соотношение для работы составляет примерно 1,80. Затем убедитесь, что глина дефлокулирована.
Что такое дефлокуляция?
В глиняный шликер необходимо добавить химикаты, чтобы он имел правильную текучесть. Это называется дефлокуляцией.Дефлокуляция заключается в том, чтобы «рассеять частицы в шликере так, чтобы для придания шликеру жидкости требовалось меньше воды». Для этого можно использовать несколько капель силиката натрия. Жидкий дефлокулянт типа Darvan тоже хорош, так как он не разъедает гипсовую форму. Носите респираторную маску на протяжении всего процесса превращения глиняного тела в комбинезон, чтобы не вдыхать вредные химические вещества.
Как вылить отливку
Как только ваш блин приобретет нужную консистенцию, вам понадобится готовая гипсовая форма.Гипсовые формы легко купить, или вы можете воспользоваться нашими советами и уловками, чтобы сделать свою гипсовую форму. Формы изготавливаются из гипса, так как они хорошо впитывают влагу.
Осторожно вылейте бланк в полость формы, гипсовая форма парижской формы начнет впитывать воду из глины и начнется процесс высыхания глины. Как только глина начнет сохнуть до подходящей толщины (время будет зависеть от размера формы, но для средней / маленькой формы должно хватить 10 минут), вы можете вылить лишнюю глиняную смесь. Выливание глиняной смеси — это умение, и делать это нужно очень осторожно. Вылейте его обратно в ведро для глиняной смеси, чтобы не потратить впустую. Во время заливки положите на ведро два деревянных бруска, чтобы на них опиралась гипсовая форма, перевернутой вверх дном, чтобы блин выливался равномерно. Некоторые гончары рекомендуют выливать шликер под углом, чтобы внутренняя поверхность была еще более гладкой. Когда все выльется, срежьте лишнюю глину с верхней части формы.
Извлечение посуды из формы
Когда кусок высохнет (время, необходимое для высыхания глины, будет зависеть от размера формы, которую вы используете), вы можете опрокинуть ее.Подставьте под форму плоскую доску и осторожно переверните. Это самый простой способ, и изделие должно аккуратно выходить, так как глина усадится в форме. Оттуда вы можете привести в порядок края, и ваше изделие будет готово к обжигу и глазурованию.
Создание фарфора
Все статьи
Недорогой тестер текучести расплава глазуриОдноскоростной лабораторный или студийный смеситель для суспензии
Учебник Конус 6 Матовая глазурь с проблемами
Регулировка расширения глазури расчетным путем для устранения дрожания
Slip Alberta, 20 лет замены для Albany Slip
Обзор керамических красителей
Контролируете ли вы свой производственный процесс?
Безопасны ли ваши глазури для пищевых продуктов или они вымываются?
Нападение на стекло: механизмы коррозионного воздействия
Глазури, корпуса, ангобы для шаровых фрез
Связующие для керамических тел
Новые возможности для борьбы с увлечением: MgO (G1215U)
Керамические глазури сегодня
Номенклатура керамических материалов
Состав керамической плитки для глиняных тел
Изменение нашего взгляда на глазури
Chemistry vs.

Концентрат на одной хорошей глазури
Конус 6 Рецепт плавающей голубой глазури
Медно-красные глазури
Образование трещин и бактерии: есть ли опасность?
Растрескивание в глазури для керамогранита: устранение причин, а не симптомов
Создание керамического шликера или ангоба без глазури
Создание собственной бюджетной глазури
Хрустальные глазури: понимание процесса и материалов
Дефлокулянты: подробный обзор
Демонстрация проблем, связанных с подгонкой глазури для Студенты
Диагностика проблемы отливки на заводе сантехники
Сушка керамики без трещин
Дублирование плафона Albany
Дублирование шамотного глина AP Green
Электрические печи для хобби: что нужно знать
Борьба с глазурованным драконом
Испытательные стержни из глины для обжига
Обжиг: что происходит Керамическая посуда в печи для обжига
Сначала вы это увидите, а потом уже нет: Устойчивость глазури Raku
Закрепление глазури, которая не остается в суспензии
Создание прозрачной глазури, совместимой с хромо-оловянными пятнами
Создание фарфора
Формулирование золы и естественного вещества -Материальные глазури
Формулирование собственного глиняного тела
G1214M Конус 5-7 20×5 Глянцевая базовая глазурь
G1214W Co ne 6 Transparent Base Glaze
G1214Z Cone 6 Matte Base Glaze
G1916M Cone 06-04 Base Glaze
G1947U / G2571A Cone 10 / 10R Base Matte / Glossy Glazes
Получение желаемого цвета глазури: работа с пятнами
Глазурь и пигменты для тела и Пятна в производстве керамической плитки
Основы химии глазури — формула, анализ, мол.
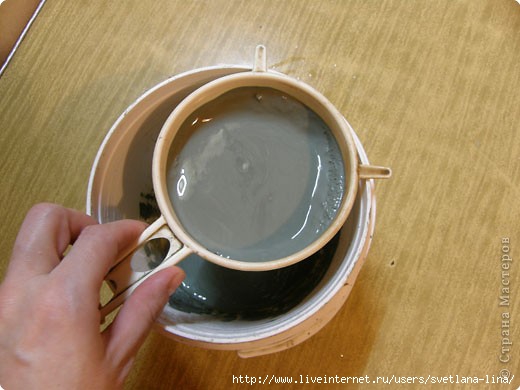
Химия глазури с использованием приблизительного анализа
Рецепты глазури: составьте собственное решение
Типы глазури, рецептура и применение в плиточной промышленности
Проверка вашей глазури на содержание токсичных металлов
Глянцевые глазури
Как проводится химический анализ материала
Как настольный компьютер INSIGHT справляется с единством, LOI и весом формулы
Как найти и проверить свои собственные природные глины
Как глазировать кружку лайнером
Я всегда так поступал!
Струйное декорирование керамической плитки
Расшифровка конусов Ортона
Безопасна ли обожженная посуда?
Конус выщелачивания 6 Пример использования глазури
Формулы предельных значений и целевые формулы
Низкобюджетные испытания свойств глазури в сыром и обожженном виде
Рецепт корпуса для отливки белого талька с низким уровнем возгорания
Сделайте свою собственную подставку для шаровой мельницы
Изготовление конусов для испытаний глазури
Monoporosa или Single Обожженная настенная плитка
Органическое вещество в глине: подробный обзор
Керамика, устойчивая к атмосферным воздействиям на открытом воздухе
Обзор бумажной глины
Покраска глазури вместо погружения или распыления
Распределение частиц керамического порошка по размерам
Керамогранит, керамическая плитка или гранитная плитка
Обоснование противоречивых мнений о пластичности
Ravenscrag скольжению рождается
Recylcing Scrap Clay
Снижения температуры обжига в глазури от конуса 10 до 6
одиночного огня Остекление
водорастворимых солей в минералах: Детальный обзор
некоторых ключей к работе с огневыми трещинами
Керамогранит Casting тело рецептов
Подставив Cornwall Камень
Супер-изысканный Terra Sigillata
Th e Химия, физика и производство глазури
Влияние подгонки глазури на прочность обожженной посуды
Четыре уровня, на которых следует рассматривать керамическую глазурь
Процесс изготовления керамической майолики
Физика глиняных тел
Молитва Гончара
Правильный химический состав для Cone 6 MgO Matte
Испытания на то, чтобы быть единственным техническим специалистом в клубе
Нытье останавливается: реалистичный взгляд на глиняные тела
Эти немаркированные мешки и ведра
Плитка и мозаика для гончаров
Токсичность огнеупорных кирпичей, используемых в печах
Торговля Рецепты глазури
Общие сведения о керамических материалах
Общие сведения о оксидах керамики
Сведения о свойствах глазури
Общие сведения о процессе дефлокуляции при шликерном литье
Общие сведения о рецептах шликерного литья терракотовой глазури в Северной Америке
Общие сведения о тепловом расширении в керамической глазури
Нежелательная кристаллизация в конусе 6 Глазурь
Пестрые глазури
Вулканический пепел
Wha t Определяет температуру обжига глазури?
Что такое крот, проверка крота
Что такое глазурованный дракон?
С чего начать?
Почему учебная глазурь такая сложная
Описание
Принципы создания фарфора довольно просты. Вам просто нужно знать назначение каждого материала, начальный рецепт и режим тестирования.
Артикул
.Невероятные успехи в производстве фарфора и оборудования для обжига были достигнуты за последние десятилетия. Робототехника и компьютерные контроллеры произвели революцию во всей керамической промышленности. Однако сами глиняные тела сопротивлялись изменениям. Хотя понимание и устранение неисправностей промышленных машин может быть обычным явлением, понимание используемых в них глин встречается гораздо реже.Динамика обработки порошка, суспензии и влажных материалов, формовки, сушки и обжига является ключевыми факторами для оптимизации производственного процесса и качества конечного продукта. Попробуем раскрыть хоть какую-то загадку из общей рецептуры фарфора.
Традиционный фарфор для функциональной посуды на самом деле представляет собой просто керамическое тело с низким содержанием Fe 2 O 3 . Общий рецепт фарфора вывести довольно легко. В отличие от глазурей, мы особо не рассматриваем химию фарфора, нас интересуют физические свойства.Давайте поговорим о создании собственного фарфора (не вдаваясь в технические подробности). Пока я говорю о изготовлении пластикового фарфора, изложенные принципы, безусловно, применимы к другим типам, просто подумайте нестандартно, когда вам нужно.
Фарфор функциональный общего назначения содержит
- Кремнезем (кварц): Он обеспечивает заполнитель для обожженной матрицы (как гравий в бетоне).
- Глина: Придает пластичность и твердость при высыхании влажным материалам и во время обжига превращается в сетку кристаллов (что придает фарфору прочность).
- Полевой шпат и нефелиновый сиенит: плавление полевого шпата заполняет пустоты между частицами кремнезема и глины и цементирует их в прочную массу.
Фарфор специального назначения может также содержать
- Глинозем: вместо диоксида кремния для меньшего расширения и более твердого обожженного материала.
- Органические отвердители: Вместо глины или в дополнение к ней (например, для пылеподавления).
- Фриц: Вместо или в дополнение к полевому шпату для достижения более низкой температуры плавления.
- Минералы с низким коэффициентом расширения: для уменьшения теплового расширения.
Самый белый и полупрозрачный фарфор изготавливается из самых дорогих и чистых материалов с низким содержанием железа. Однако для некоторых применений не требуется высокая степень белизны, для этих более дешевых или более доступных глин и полевых шпатов могут использоваться.
По рецепту «Universal 25 Porcelain» обычно получается недорогой не очень белый фарфор с конусом 10, имеющий умеренную пластичность и почти нулевую пористость (в зависимости от конкретных свойств ингредиентов).Он состоит из 25% шариковой глины, каолина, полевого шпата и кремнезема, или, проще говоря, 50% глины и 25% кремнезема и полевого шпата. Тысячи гончаров и компаний используют его «как есть» или изменяют его в соответствии с конкретными материалами или обстоятельствами. Давайте рассмотрим некоторые физические свойства, которые нужно искать в фарфоре (без какого-либо конкретного заказа).
- Зрелость: водопоглощение (или пористость) является наиболее распространенным показателем зрелости. Чаще всего стремятся к нулевой пористости. Усадка в огне также является хорошим показателем зрелости, поскольку тела созревают и уплотняются в печи, они сокращаются до минимума, а затем начинают расширяться и раздуваться при чрезмерном обжиге.Полупрозрачный фарфор с высокой степенью стекловидности может иметь общую усадку более 15-18% (от обожженного до обожженного), тогда как изделия из белого стекла (с пористостью 0-1%) имеют усадку около 12%. Целесообразно задавать температуру обжига тела, зная о его зрелости, в диапазоне температур ниже и выше.
- Светящаяся полупрозрачность: мы все этого хотим. Но за это приходится платить. Полупрозрачный фарфор сильнее плавится, поэтому больше коробится. Для них требуется больше полевого шпата и меньше и более белых глин (обычно только каолин) с низким содержанием TiO 2 , что означает, что они менее пластичны и более дороги.
Вы можете сравнить прозрачность обожженного фарфора, обжигая очень тонкие ломтики (толщиной 2 мм), наклеивая их на картон с дырками, а затем держа на свету.
- Последовательность. Это продемонстрирует только контроль качества в течение нескольких лет. Обратите внимание на различия в усадке при сушке, характеристиках сушки, пористости и усадке после обжига, а также в цвете и характере обжига и попытайтесь связать изменения с конкретным сырьем. Различные компании, производящие каолин и шариковую глину, демонстрируют различные обязательства и отношение к сохранению физических свойств своих материалов для керамической промышленности.Бентониты требуют особого внимания на предмет наличия железных пятен.
- Пластичность. Это можно определить по усадке при высыхании и оценить физически, сравнив удобоукладываемость. Высокопластичный фарфор может иметь усадку при высыхании до 7%, а у фарфора с галлуазитом — еще больше. Пластичность может быть придана (после достижения обжиговых свойств) добавлением бентонита (доступно множество различных).
- Эффективность сушки. Фарфор часто имеет тенденцию к растрескиванию при высыхании, он не обладает прочностью в сыром виде, как изделия из керамики, и может иметь очень высокую усадку при высыхании, если он содержит значительные добавки пластификатора.Используйте испытание на ускоренный градиент высыхания (например, DFAC), чтобы охарактеризовать это свойство.
- Прочность в огне и сухом состоянии. Фарфор обычно имеет низкую прочность в сухом состоянии, но высокую прочность в огне. Существует множество способов сравнить сильные стороны разных фарфора (используйте свою изобретательность и лабораторное оборудование, если оно у вас есть).
- Speck Development — Соблюдайте это при обжиге посуды, особенно при восстановительном горении. Примеси могут появляться в различном сырье, но особенно в шариковых глинах и бентонитах, следите за этим, промывая материал через сито 200 меш.
- Растворимые вещества. Шариковые глины, бентониты и иногда каолины часто содержат растворимые соли, сульфаты кальция и магния, которые мигрируют на поверхность с водой во время сушки и оставляют видимую пленку на поверхности после сушки и обжига.
Используйте тест SOLU, чтобы определить, является ли это проблемой.
- Устойчивость к тепловому удару. Это относится к способности обожженной глины выдерживать температурные градиенты (внезапные изменения температуры одной части куска) без образования трещин. Если это свойство важно для вас, сравните тела с помощью теста на погружение в пламя или ледяную / кипящую воду.Хорошая подгонка глазури действительно может повлиять на способность посуды выдерживать термический удар без образования трещин.
- Легкость нанесения глазури. Некоторые фарфоры увлекаются глазурью гораздо больше, чем другие, особенно если посуда подвергается резкому охлаждению после нагрева. На фарфор с высоким содержанием кремнезема легче подобрать глазури. Фарфор с более низким содержанием кремнезема в рецепте имеет больше места для полевого шпата и, таким образом, может быть более остеклован, однако вам нужно знать, как уменьшить тепловое расширение ваших глазурей, чтобы они подходили.
- Обожженная белизна.
Возможен бумажный белый фарфор. Супербелые каолины и пластификаторы, не содержащие железа, — замечательные материалы, но они намного дороже.
- Волатильность срабатывания. Если, например, требуется прозрачность, обычно необходимо сформулировать тело так, чтобы оно было достаточно мягким для достижения желаемой прозрачности, но не настолько, чтобы оно чрезмерно коробилось. Диапазон заданных температур может быть довольно узким, поэтому необходим хороший контроль стрельбы.
- Поверхностный характер. Самые приятные поверхности — самые остеклованные. Это означает, что рецепт должен содержать как можно больше полевого шпата.
Фарфор можно сравнить во всех вышеперечисленных областях. По логике, у вас не может быть лучшего из них. Всегда есть компромиссы, компромиссы, особенно если вы не хотите, чтобы это было слишком дорого. Все эти физические свойства можно измерить или, по крайней мере, сравнить с помощью простого оборудования, методов и наблюдений, как описано в области испытаний на этом сайте. Давайте посмотрим на каждый из материалов в рецепте, чтобы понять их функции и то, как их можно изменить.
Каолин
Настоящий фарфор обычно получает всю свою пластичность от каолина. Поскольку каолины часто имеют ограниченную пластичность, это ограничивает технологичность метания или моделирования фарфора из них. Тем не менее, есть несколько удивительно пластичных каолинов, хотя ограниченный диапазон размеров частиц может означать менее чем идеальные характеристики сушки. Не соглашайтесь с тем, что каолин пластиковый только потому, что в его названии есть слово «пластик» или поставщик говорит, что это пластик, проверьте себя.Для литья фарфора вполне возможен полностью каолиновый подход (с использованием 50% каолина, а не 25% каолина и 25% шариковой глины), поскольку эти тела значительно выигрывают от уменьшенной усадки при сушке и повышенной водопроницаемости, связанной с большим размером частиц каолинов. . Однако фарфор, полностью изготовленный из каолина, может не иметь прочности, чтобы оторваться от гипсовой формы без трещин, при необходимости добавьте немного пластификатора.
Каолины могут сильно различаться по зрелости. Британские каолины требуют использования меньшего количества полевого шпата, потому что в них уже есть естественные флюсы в составе слюдяного минерала, который они содержат.Таким образом, даже если они могут быть менее пластичными, требуется меньше флюса, поэтому в рецепте можно использовать больше каолина. Хорошая идея состоит в том, чтобы добавлять каолин в рецепт с использованием более чем одной марки, это обеспечивает лучшее распределение конечных размеров частиц и сводит к минимуму воздействие на организм при изменении одного каолина.
Поскольку каолины довольно сильно различаются по своей пластичности, зрелости, растворимым солям, размеру частиц и белизне, испытать и классифицировать их все может быть довольно сложно. Таблицы данных часто не так полезны, потому что они представляют информацию по-разному, и компания редко объясняет свои материалы с точки зрения других хорошо известных альтернатив.Таким образом, бремя выбора лучших каолинов возлагается на вас и вашу способность оценивать и сравнивать их с помощью тестов, которые документируют соответствующие физические свойства. Мы рекомендуем вам использовать тесты DFAC, SHAB и LDW для оценки каолинов и шариковых глин.
Каолины с большим размером частиц, как правило, более грязные, менее пластичные, более дорогие и имеют более низкую прочность в сухом состоянии, поэтому их преимущества требуют затрат. Из обычных легких горящих каолинов, таких как EPK, можно изготавливать довольно быстро забрасываемые тела из глины с нулевым шаром.Некоторые люди используют каолин с крупными частицами, когда в их смеси также есть шариковая глина, последнее может сводить на нет преимущество первого! Конечно, также доступны глины с крупными шариками, но помните, что они все же значительно мельче стандартных каолинов. Кроме того, тонкая настройка смеси каолина не имеет смысла, если тело не дефлокулируется должным образом. Лучше всего использовать стандартный белый каолин, правильно его дефлокулировать и научиться работать с ним. Затем выполните точную настройку, заменив материал с крупными частицами на скорость разливки, наблюдая за появлением любых вредных свойств.
Ниже приводится образец отчета Foresight по каолину (Foresight был предшественником insight-live.com). Я тестировал тесты DFAC, SHAB, LDW и SIEV.
ОТЧЕТ ПО ТЕСТОВЫМ ДАННЫМ ДЛЯ ЗАПУСКА ======================================== НОМЕР: L2497 ОПИСАНИЕ: K&T DIAMOND KAOLIN ДАТА: 27.07.93 РАСПОЛОЖЕНИЕ: BD 725 ======================================== Это монтмориллонитовый материал с промежуточным размером частиц. Я получил этот образец 7/93 для тестирования, чтобы сравнить его с каолином Pioneer.У него на 1-2% меньше усадка в огне и на 4-5% выше абсорбция. при более высокой температуре, чем пионерский каолин. Цвет выстрела аналогичен. Этот каолин был бы ценен для улучшения нашего организма. для минимизации сдвига при изменении одного материала. КОЭФФИЦИЕНТ СУШКИ (ID-DF, ABBR-DFAC) DRY_FAC - A000 LOI / содержание воды (ID-LW, ABBR-LDW) WET-WT DRY-WT FIRE-WT OIL-WT IMM-WT ПРОЦЕНТНАЯ ПЛОТНОСТЬ LOI + ------- + ------- + - ------ + ------- + ------ + 1 | 25.99 | 15.03 | 13.10 | 15.53 | | 42,2% 12,8% 1,00 г / см + ------- + ------- + -------- + ------- + ------ + УСИЛЕНИЕ / ПОГЛОЩЕНИЕ / h3O (ID-SA, ABBR-SAWL) DRY-LEN FIR-LEN FIRE-WT BOIL-WT КОНУС FIRE-SHR DRY-SHR ABSORP + ------- + ------- + ------- + ------- + ----- + 6 | 96,3 | 89,4 | 31,68 | 36,61 | 6,4 | 7,17% 3,7% 15,6% 7 | 96,17 | 88,43 | 31,87 | 35,98 | 7,0 | 8,05% 3,8% 12,9% 8 | 96,15 | 88,16 | 32,65 | 36,59 | 7,4 | 8,31% 3,8% 12.1% 9 | 96,18 | 86,29 | 31,09 | 33,37 | 8,9 | 10,28% 3,8% 7,3% 11 | 96,38 | 86,2 | 30,96 | 33,16 | 10,8 | 10,56% 3,6% 7,1% 12 | 96,39 | 86,42 | 32,74 | 35,52 | 10,0R | 10,34% 3,6% 8,5% + ------- + ------- + ------- + ------- + ----- + РАСТВОРИТЕЛИ (ID-SL, ABBR-SOLU) ГЛИНА ГЛАЗЬ-ГЛИНА СУХАЯ ГЛИНА + ---------- + --------- + ------- + 1 | NIL | | NIL | + ---------- + --------- + ------- + АНАЛИЗ SEIVE (ID-SV, ABBR-SIEV) TOTAL PLUS-35 PLUS-48 PLUS-65 PLUS-100 PLUS-150 PLUS-200 PLUS-325 + ------ + ------- + ------- + ------- + -------- + -------- + -------- + -------- + 1 | 100 | | | | | .
01 | .04 | .6 | + ------ + ------- + ------- + ------- + -------- + -------- + -------- + -------- +
Шариковая глина и бентонит
Глина для мячей намного тоньше и, следовательно, более пластична, чем каолин. Доступен очень широкий ассортимент шариковых глин, некоторые из них намного пластичнее. Белые горящие шариковые глины часто не имеют пластичности, близкой к своим более грязным аналогам. Бентонит намного мельче шаровидной глины (конечные частицы намного меньше). Он невероятно пластичен, добавление всего 2% в рецепт может кардинально улучшить рабочие свойства.Однако у этих материалов есть и обратная сторона. Шариковые глины могут содержать в десять раз больше коричневого окиси железа, чем каолин, и многие из них содержат тяжелые растворимые соли, которые образуют темную пену на обожженной поверхности. Многие также содержат частицы лигнита, которые могут привести к дефектам глазури. Сырые бентониты могут быть совершенно грязными, ярко-коричневыми или красными с возможными пятнами и растворимыми солями, иногда такими тяжелыми, что они образуют глазурь. Белые бентониты для обжига бывают самых разных пластмасс. У некоторых так мало пластичности, что вы удивитесь, зачем их использовать для керамики, другие невероятно пластичны.Но будьте осторожны, даже если вам может потребоваться всего 3-5%, стоимость одного этого материала может быть больше, чем остальные 95% вместе взятые! Изучение всех доступных вам шариковых глин и бентонитов может стать настоящим образованием! Опять же, очень важно, чтобы у вас была четко определенная программа тестирования для сравнения этих материалов (например, то, что вы можете администрировать в учетной записи на https://insight-live.com). Стоит упомянуть еще один положительный момент шаровой глины. Шариковые глины содержат свободный кремнезем, поэтому, если в рецепте присутствует значительное количество шаровидной глины, вы можете уменьшить количество кремнезема, и это оставляет место для добавления большего количества глины для пластичности или полевого шпата для созревания.
Ниже приводится образец отчета для шариковой глины:
======================================== НОМЕР: L2553D ОПИСАНИЕ: ШАРОВАЯ ГЛИНА GLEASON ДАТА: 29.04.94 РАСПОЛОЖЕНИЕ: BD 763 ======================================== Смешанный кальцин 50:50: сырой. Он довольно белый в сыром виде и намного пластичнее, чем 49'r. Обожженные бруски - самые белые из шаров, испытанных в этом раунде, и Очень чистый. На 10р есть небольшая коричневатая накипь, но это очень красивый шаровой пластилин, хотя он дает гораздо больше усадки.Это очень огнеупорная шаровая глина. КОЭФФИЦИЕНТ СУШКИ (ID-DF, ABBR-DFAC) DRY_FAC - A000 | LOI / содержание воды (ID-LW, ABBR-LDW) WET-WT DRY-WT FIRE-WT OIL-WT IMM-WT ПРОЦЕНТНАЯ ПЛОТНОСТЬ LOI + ------- + ------- + -------- + ------- + ------- + 1 | 33,58 | 24.22 | 22,82 | 24,57 | 8.94 | 27,9% 5,8% 1,57 г / см + ------- + ------- + -------- + ------- + ------- + УСИЛЕНИЕ / ПОГЛОЩЕНИЕ / h3O (ID-SA, ABBR-SAWL) DRY-LEN FIR-LEN FIRE-WT BOIL-WT КОНУС FIRE-SHR DRY-SHR ABSORP + ------- + ------- + ------- + ------- + ----- + 5 | 94.81 | 84,65 | 35,1 | 37,8 | 9,8 | 10,72% 5,2% 7,7% 6 | 94,81 | 86.
05 | 38,70 | 43.15 | 6.3 | 9,24% 5,2% 11,5% 7 | 94,8 | 85,1 | 37.07 | 40,65 | 6.9 | 10,23% 5,2% 9,7% 8 | 94,9 | 85.03 | 35,52 | 38,68 | 8.3 | 10,40% 5,1% 8,9% 9 | 94.94 | 84.18 | 33,47 | 35,99 | 8,8 | 11,33% 5,1% 7,5% 11 | 94,79 | 84,13 | 32.31 | 34,79 | 10,7 | 11,25% 5,2% 7,7% 12 | 94,85 | 84,51 | 32.24 | 35.01 | 10R | 10,90% 5,2% 8,6% + ------- + ------- + ------- + ------- + ----- + РАСТВОРИТЕЛИ (ID-SL, ABBR-SOLU) ГЛИНА ГЛАЗЬ-ГЛИНА СУХАЯ ГЛИНА + ---------- + --------- + -------- + 1 | MED | | MED | + ---------- + --------- + -------- + АНАЛИЗ SEIVE (ID-SV, ABBR-SIEV) TOTAL PLUS-35 PLUS-48 PLUS-65 PLUS-100 PLUS-150 PLUS-200 PLUS-325 + ------ + ------- + ------- + ------- + -------- + -------- + -------- + -------- + 1 | 100 | | | .01 | .01 | .03 | .28 | 1.1 | + ------ + ------- + ------- + ------- + -------- + -------- + -------- + -------- +
Итак, самое простое, что вы можете сделать со стандартным рецептом «25 Porcelain», чтобы увеличить его пластичность, — это добавить 2–3% сырого бентонита. Несмотря на то, что самые недорогие бентониты размером 200 меш могут быть довольно грязными, это небольшое количество может не так сильно повлиять на цвет обожженного материала, как вы могли ожидать. Даже если бентонит содержит 5% железа, добавление 5% его в рецепт добавляет всего 0,25% железа в организм в целом.Не упускайте из виду одну деталь: в одном мешке с бентонитом не должно быть частиц железа, а в другом -. Переработчики бентонита обычно гарантируют, что определенный процент частиц меньше 200 меш, но они не определяют, что такое более крупный материал. Вы можете купить сырые бентониты тонкой керамики (например, 600 меш), они намного дороже, но вы никогда не получите обожженных пятнышек. Если белизна не имеет первостепенного значения, вы можете увеличить количество шариковой глины за счет каолина, чтобы получить пластиковую белую посуду (но вам может потребоваться также уменьшить количество полевого шпата, поскольку шариковая глина менее огнеупорная, чем каолин).Если вам нужен очень белый фарфор, вам нужно решить задачу уменьшения или полного отказа от шариковой глины.
Там, где супер белизна вторична по отношению к хорошему телу общего назначения, обычно можно терпеть немного глины. Если самое важное — иметь максимально пластичный корпус, тогда вы будете использовать только шариковую глину, а не каолин (например, B-Mix от Laguna).
Полевой шпат
Это флюсы, или, вернее, содержат флюсы. Флюсы — это оксиды, которые способствуют развитию обожженной зрелости за счет разжижения и медленного растворения некоторых из глины и кремнезема.Необходимое общее количество флюса легко определить простым обжигом в диапазоне температур выше и ниже той, в которой вы собираетесь работать; изучение кривых усадки, прочности и усадки при обжиге; и регулирование количества полевого шпата для достижения желаемой зрелости. Количество полевого шпата для тела конуса 10 варьируется от 15% до 30%, в зависимости от содержания флюса в других материалах в рецепте. Для типичного американского каолина требуется около 25% для конуса 10 и до 50% для конуса 6.
С полевыми шпатами могут быть проблемы. В то время как некоторые бренды могут быть относительно свободными от железа, другие стреляют удивительно темнее. Некоторые из них могут вызывать проблемы флокуляции из-за низкой растворимости (например, нефелиновый сиенит). Натриевые полевые шпаты, как правило, более чистые и эффективные. По возможности используйте два или три вместе (чтобы смягчить изменения, которые могут произойти в одном).
Кремнезем
Кремнезем — очень прочный и недорогой материал. Зерна кварца действуют прежде всего как микроагрегат или каркасная структура для обожженной матрицы.Кроме того, часть кремнезема растворяется флюсами с образованием алюмосиликатного стекла. Слишком много кремнезема в рецепте может означать более низкую пластичность (поскольку для глины остается меньше места). Однако есть также много дискуссий о вредном воздействии кристобалита (например, обжига), развитие которого во время высокотемпературного обжига связано с доступным свободным кварцем. Таким образом, есть определенные преимущества в снижении количества кремнезема, особенно если у вас есть возможность отрегулировать свои глазури, чтобы снизить их расширение. Использование меньшего количества диоксида кремния означает, что можно добавить больше глины, что приведет к более высокой пластичности. Более мелкий кремнезем (300 меш) лучше реагирует с флюсами, поэтому его требуется меньше. Слишком мало кремнезема в теле может означать образование трещин в глазури, так как кварцевый минерал способствует низкому расширению, что способствует подгонке глазури. Конечно, недостаток кремнезема также будет означать большую тенденцию к деформации во время обжига. Для конуса 10 многие технические специалисты стремятся к 20-25% по причинам расширения и обеспечения стабильности обжига в широком диапазоне температур.
Рецепты и стратегии
Большинство людей отметили, что рецепт «25 Porcelain» имеет недостатки, которые можно исправить в зависимости от ситуации и материала. Чтобы улучшить этот рецепт для конуса 10:
- Заменить шар глины на весь пластиковый каолин
- Добавьте немного бентонита, чтобы получить необходимую пластичность (будьте готовы к большей усадке при высыхании)
- Диверсифицируйте глины и полевой шпат, используя по 2 или 3 вида каждого (чтобы рецепт был устойчивым к изменениям в отдельных материалах)
- Пробный огонь, чтобы увидеть, нужно ли вам увеличивать или уменьшать зрелость и регулировать соотношение полевого шпата иглина соответственно.
Для создания белого полупрозрачного конуса, 6 фарфор из полевого шпата:
- Начните с 20% кремнезема для глазури
- Добавьте 40% полевого шпата для созревания (нефелиновый сиенит или минспар очень белые)
- Добавьте 40% самого белого каолина, который вы можете получить (новозеландский гекторит — лучшее, о чем мы знаем)
- Добавьте 3-5% самого белого бентонита или гекторита, который вы можете получить (Veegum — лучшее, о чем мы знаем)
- Сделайте пробную смесь и оцените пористость, эффективность сушки и удобоукладываемость
- Добавьте или уменьшите количество пластификатора по мере необходимости
- Увеличьте количество полевого шпата за счет каолина для большей зрелости, сделайте наоборот, если он перегорел сверх нормы
- Проверьте еще раз и повторите.
Если вам нужно создать фарфор для литья, помните, что требуется гораздо более низкая пластичность. В промышленности принято считать, что гораздо важнее использовать каолины с крупными частицами, чтобы вода могла легко вытягиваться гипсовой формой. Однако для небольшой операции, которая не требует действительно оптимизации времени отделения от формы, подойдут обычные каолины. Самые чистые каолины и шарики из глины также наименее пластичны, поэтому отливка фарфора (которая может терпеть это) может обеспечить более белый и более полупрозрачный эффект, чем их пластмассовые аналоги.Крайне важно, чтобы вы понимали принципы «дефлокуляции», чтобы можно было минимизировать количество воды в суспензии и добиться надлежащего отделения формы и времени заливки. Если вы не были свидетелями волшебства добавления нескольких капель диспергатора в безнадежно густую смесь глины и воды, не вызывающую беспокойства, вы не выжили! Если вам нужно отлить очень тонкую посуду, вам, возможно, придется добавить в суспензию немного бентонита (начните с 1%), чтобы дать ей силу оторваться от формы во время сушки.
Если вы изготавливаете пластмассовый фарфор для моделирования, метания или машинной формовки; обратите особое внимание на его сушильные свойства. Поскольку фарфор мелкозернистый, он обычно плохо сохнет, поэтому пластиковый фарфор еще хуже. Добавьте достаточно бентонита, чтобы придать ему необходимую пластичность, но не настолько, чтобы при высыхании посуда потрескалась. Важно провести хороший тест для оценки и сравнения характеристик сушки (см. Тест DFAC в разделе «Тесты» на этом сайте). Некоторые люди добавляют в фарфор молохитовый грог для лучшего высыхания, но не думают, что это сработает, пока вы сами не попробуете.
Независимо от того, какой вид фарфора вы производите, тщательно продумайте, насколько он должен быть зрелым. Если нулевая абсорбция не требуется, подумайте об уменьшении количества полевого шпата, чтобы добиться большей пластичности глин (и иметь возможность уменьшить количество бентонита). Такое тело все еще можно считать функциональным и стекловидным, и оно будет сопротивляться деформации в печи. Кроме того, материальные изменения, которые приводят к большей зрелости, с меньшей вероятностью вызовут проблемы в организме, у которого есть «пространство для движения». Когда вы оцениваете поглощение в огне, измеряйте свойство при различных температурах.Философия «измерения только при рабочей температуре» — это подход туннельного зрения, который почти наверняка доставит вам неприятности, особенно в ситуациях, когда рабочая температура намного выше точки, при которой достигается нулевая пористость. Например, если ваше тело достигает нулевой пористости в конусе 8, выстрел в конус 10 вызовет у вас много головных болей из-за деформации.
Да, мы коснулись только поверхности, но для хорошего старта этого, конечно, достаточно. Таким образом, я подготовил следующую диаграмму.В нем перечислены некоторые компромиссы, которые вы должны учитывать при составлении или настройке керамического фарфора.
Материал | Типичный% | Детали |
Кремнезем | 20% -25% | Используйте не менее 20% (если только у вас нет глазурей с очень низким коэффициентом расширения).![]() Используйте самый мелкий размер частиц, чтобы уменьшить необходимое количество.Попробуйте кальцинированный оксид алюминия в качестве заменителя, чтобы получить более прочный (но более дорогой) продукт. Используйте расчет, чтобы уменьшить расширение ваших глазурей и уменьшить содержание кремнезема. |
Флюс | Корпус из полевого шпата Конус 10: 25% полевого шпата Конус 6: 35% полевого шпата Корпус из фритты | Полевой шпат (и нефелиновый сиенит) на сегодняшний день являются наиболее распространенными флюсами. Требуемый процент зависит от того, что вы хотите.Используйте количество, необходимое для степени стеклования, необходимой при температуре, при которой вы хотите обжигать.![]() Измерьте зрелость с помощью тестов, определенных на сайте insight-live.com (абсорбция, усадка в огне и прочность в диапазоне температур), и отрегулируйте до необходимого количества. Попробуйте разные полевые шпаты (включая нефелиновый сиенит), смеси полевых шпатов и фритты или просто фритту, чтобы достичь желаемого компромисса между зрелостью, белизной и стоимостью. |
Каолин | Конус 10: 25% -50% Конус 6: 20% -40%. | В идеале используйте как можно больше каолина и как можно меньше шариковой глины (для обжига белизны). Испытайте как можно больше типов, чтобы найти наилучшее сочетание белизны и пластичности. Английские каолины менее пластичны (и более дороги), но также способствуют большей зрелости.![]() |
Шариковая глина | До 25% | Шариковые глины содержат больше железа и ухудшают белизну после обжига. Используйте их как менее дорогие источники пластики. Более высокий процент шариковой глины замедляет высыхание и может увеличить количество трещин при высыхании.Если важны белизна или прозрачность, используйте только каолины (с добавлением пластификаторов). Проведение подробных сравнений обжига и технологичности торговых марок действительно может окупиться. При необходимости добавьте 0,3% карбоната бария (для пропорции шариковой глины) для осаждения растворимых веществ, вызывающих образование накипи.![]() |
Пластификаторы | Пластиковые тела: 2-4% Отливки: 0-1% | Доступен широкий ассортимент.Бентониты самые дешевые. Наиболее дорогими являются смектиты и гекториты с высокой степенью обработки. Продукты самого высокого качества в двадцать или тридцать раз дороже самых дешевых (но вы получаете то, за что платите). Проведите тесты, чтобы сравнить варианты и найти компромисс между воздействием на цвет обжига и полученной пластичностью. Проверьте эффективность сушки, вздутие, образование пятен, растворимость и консистенцию марки, которую вы будете использовать. В фарфоре высочайшего качества используются очень белые непластичные глины, а это означает, что этот компонент имеет решающее значение для получения необходимых рабочих свойств.Если деньги не имеют значения, используйте новозеландский галлуазит с VeeGum в качестве пластификатора и фритту 3110 в качестве флюса (это даст вам большую гибкость для максимального увеличения количества кремнезема для глазури).![]() |
Костяной фарфор
Их обжигают при температуре 1250 ° C и глазируют при температуре от 1050 до 1100 ° C. Один известный нам состав — это 45% кости, 30% глины и 25% смеси калийного полевого шпата и кварца. Но также используются версии с более низкой костью, она составляет всего 10% (глина такая же, но полевой шпат, очевидно, должен быть намного выше).Не совсем понятно, почему компании просто не добавляют в фарфор фритту, чтобы добиться большей прозрачности. Если вы это знаете, напишите мне.
Отражение
При обжиге фарфора происходит не просто постепенное плавление. Полевой шпат образует жидкую фазу, в которой растворяется часть каолина (и кварца), но также в которой кристалл каолина превращается в другую форму другой формы, минералогии и, что удивительно, более высокой температуры плавления. Эта кристаллическая матрица, соединенная полевым шпатом стекла на кремнеземном каркасе, создает невероятную твердость и прочность, которые может иметь фарфор. Чтобы все это произошло, вам нужен хороший режим тестирования и хорошее место для отслеживания вашей работы. Где? Аккаунт на Insight-live.com.
Связанная информация
Это полупрозрачный фарфор!
Это две конические кружки из прозрачного глазурованного фарфора на 6 конусов с лампочкой внутри. Слева — фарфоровый Plainsman M370 (у Laguna B-Mix 6 аналогичная непрозрачность). Справа — новозеландский фарфор на основе каолина с нулевой пористостью под названием Polar Ice (от Plainsmanclays.com тоже)! Секрет изготовления такого белого и полупрозрачного пластикового фарфора заключается не только в каолине Новой Зеландии, но и в использовании очень дорогого пластификатора VeeGum T, позволяющего максимально использовать полевой шпат для достижения зрелости после обжига.
Cone 6 фарфор под мрамор и метание
Эти чаши были изготовлены Тони Хансеном из смеси белого и окрашенного новозеландского каолинового фарфора (Plainsman Polar Ice), обстрелянного по конусу 6. Корпус не только белый, но и очень полупрозрачный.
Отливка с толщиной стенки всего 1 мм? NZ Kaolin + VeeGum банка.
Эта литая чаша (только что извлеченная и высушенная) имеет диаметр 130 мм и глубину 85 мм, а толщина стенок составляет всего 1 мм, а ее вес составляет всего 89 г! Шликер находился в форме всего 1 минуту. Какой промах? Полупрозрачный фарфор с конусом 6 на основе новозеландского галлуазита. Этот новозеландский материал отлично подходит для отливки шликеров (ему также требуется немного дополнительного пластификатора, чтобы тело могло отрываться от поверхности формы при усадке).
Две причины, по которым рецепты фарфора нуждаются в диоксиде кремния
Это 70% каолина и 30% полевого шпата.Обстреляли конус 6 глазурью G2926B. Обожженное тело имеет красивую фарфоровую поверхность. Но прямо из печи он так безумен! Плотный узор в виде увлечения указывает на очень серьезную проблему с посадкой. Тепловое расширение смеси каолин: полевой шпат слишком мало. Добавление 25% диоксида кремния с низким коэффициентом расширения решит проблему. Другая проблема связана с плоской формой частиц каолина. В процессе метания преобладающие частицы каолина располагаются концентрично относительно центра. Во время сушки и особенно обжига поперек них усадка больше, чем вдоль них.Все десять чашек треснули вот так! В раствор добавляется наполнитель с закругленными частицами для разделения пластин каолина. Кремнезем идеален, если использовать те же 25% добавки. Зерна действуют как заполнитель в бетоне, укрепляя матрицу и разделяя частицы глины, заставляя их ориентироваться более хаотично.
ссылок
Как сделать фарфоровые куклы
Фарфоровые куклы обычно ассоциируются со старинными куклами. Сегодняшние производители, которые делают этих кукол для коллекционеров, делают репродукции.Репродукция фарфоровой куклы стоит гораздо дешевле настоящего антиквариата. Многие фарфоровые куклы, которые производятся в наши дни, производятся в Китае, хотя у Мари Осмонд есть компания, которая производит фарфоровые куклы различных размеров, от крошечных до очень больших. Есть множество стилей и размеров, которые можно купить. К ним относятся женщины, девочки, мальчики и мужчины. Голова и конечности могут быть изготовлены из фарфора с матерчатым телом или кукла может быть полностью из фарфора. Каждая кукла индивидуализирована с использованием одежды, аксессуаров и макияжа.Изготовление одной из этих кукол с нуля — процесс долгий, тонкий и сложный.
Шаг 1. Какой тип фарфоровой куклы?
Решите, какого размера куклу вы хотите сделать: девочку, мальчика, женщину или мужчину. Размер приобретаемой вами формы будет зависеть от размера куклы, которую вы будете делать. Также необходимо решить, будет ли он полностью фарфоровым или будет мягким.
Решите, какого цвета будет фарфоровый блеск: белый, слоновая кость, телесный, розовый, восточный, персиковый, коричневый или черный.Фарфоровая шликер — это глина, которую разбавляют и процеживают до однородного состояния. Именно из него будут изготовлены все фарфоровые детали куклы.
Шаг 2 — Изготовление фарфоровой головки Изготовьте фарфоровую накладку в соответствии с инструкциями производителя. Вылейте его в форму, убедившись, что она полностью заполнена.
После заполнения формы вы поместите ее в печь и обжигаете примерно 8 часов. Не сжигайте дольше, так как это может вызвать ожог или трещину на фарфоре.Выньте форму из печи и дайте ей полностью остыть. Когда он остынет, аккуратно выньте фарфор из формы и отшлифуйте его ультратонкой наждачной бумагой, пока все края не станут гладкими. Вытрите лишнюю пыль.
Шаг 3 — Раскрашивание головыИспользуя кисть, нарисуйте всю голову акриловой краской, используя цвет, который вы выбрали для куклы. Для получения желаемого эффекта может потребоваться второй слой. Нарисуйте губы, ногти и ногти на ногах и наметьте глаз.Если вы рисуете вокруг глаз куклы, используя более глубокий цвет краски с помощью тонкой кисти, вы получите драматический эффект. Нанесите на губы прозрачный глянцевый слой краски, чтобы они выглядели увлажненными.
Шаг 4 — Аксессуары Вставьте стеклянные глазки в гнезда. Наклеиваем накладные ресницы над глазами каплей суперклея. Размер накладных ресниц, которые вы будете использовать, зависит от типа куклы, которую вы делаете; у детей ресницы обычно короче и тоньше, чем у взрослых.
Волосы могут быть из купленного вами парика или вы можете их накрасить. Если вы решите использовать парик, вы прикрепите его к голове с помощью суперклея. Если вы ищете более реалистичный эффект, вы можете укоренить волосы, прикрепляя их по одной прядке за раз тонкой иглой.
Шаг 5 — Сборка фарфоровой куклыВ этом примере мы выбрали мягкое тело, сделанное из муслина. Для утяжеленной куклы перед добавлением начинки на нижнюю часть туловища следует положить фасоль.Набейте туловище ватином или, если вы хотите позировать куклу, вам понадобится арматура.
Соедините руки и ноги с телом. Вы можете сделать это, разместив конечности в специально предназначенных для этого местах, или вы можете использовать клей или крючки, чтобы прикрепить их.